In the realm of chemical and biological pharmaceutical equipment, optimizing the performance of essential tools like the rotary evaporator, or rotovap machine, is crucial for efficiency and productivity. One significant aspect of enhancing rotovap functionality is increasing its solution capacity. This article provides a comprehensive guide on how to expand the solution capacity of rotovap machines, thereby maximizing their utility and effectiveness in various industries, including research laboratories, pharmaceutical manufacturing, and chemical synthesis.
Understanding Solution Capacity in Rotovap Machines:
Before delving into strategies for increasing solution capacity, it's essential to understand what solution capacity entails in the context of rotary evaporators. Solution capacity refers to the maximum volume of solvent that can be processed in a single operation or batch using the rotovap machine. This capacity is primarily determined by the size of the rotating flask, which holds the sample solution during the evaporation process. Increasing solution capacity involves strategies aimed at accommodating larger volumes of solvent for more efficient processing.
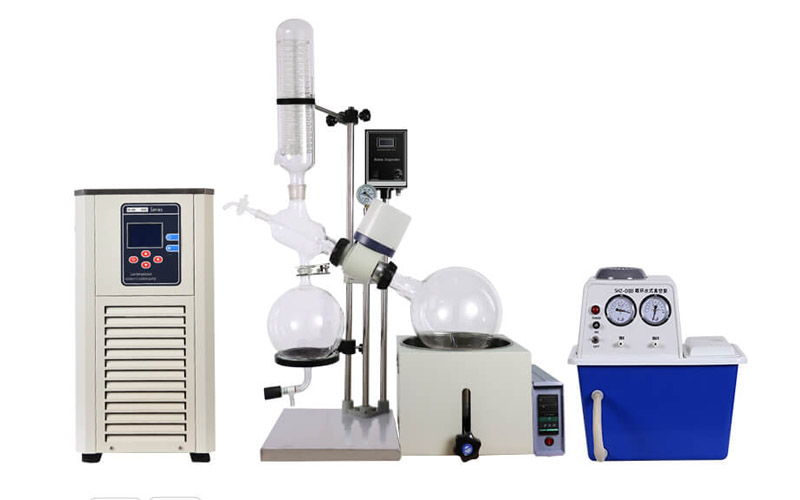
Strategies for Increasing Solution Capacity:
1. Upgrading to Larger Rotating Flasks:
One of the most straightforward methods for increasing solution capacity is to upgrade to larger rotating flasks. Rotovap machines are available with a range of flask sizes, typically measured in liters. By selecting a larger flask size, operators can process larger volumes of solution in each batch. When considering a flask upgrade, it's essential to ensure compatibility with the existing rotovap setup, including the heating bath and condenser.
Model |
Evaporating flask(L) |
Recovery flask(L) |
RE-201D |
2 |
1 |
RE-301 |
3 |
2 |
RE-501 |
5 |
3 |
RE-1002 |
10 |
5 |
RE-2002 |
20 |
10 |
RE-5002 |
50 |
20 |
2. Implementing Multi-Flask Systems:
For facilities with high throughput requirements, implementing multi-flask systems can significantly enhance solution capacity. Multi-flask systems feature multiple rotating flasks connected to a single rotovap setup, allowing operators to process multiple samples simultaneously. This approach maximizes efficiency by reducing processing time and increasing overall productivity. Advanced rotovap models offer precise control over temperature and vacuum conditions for each flask in a multi-flask system.
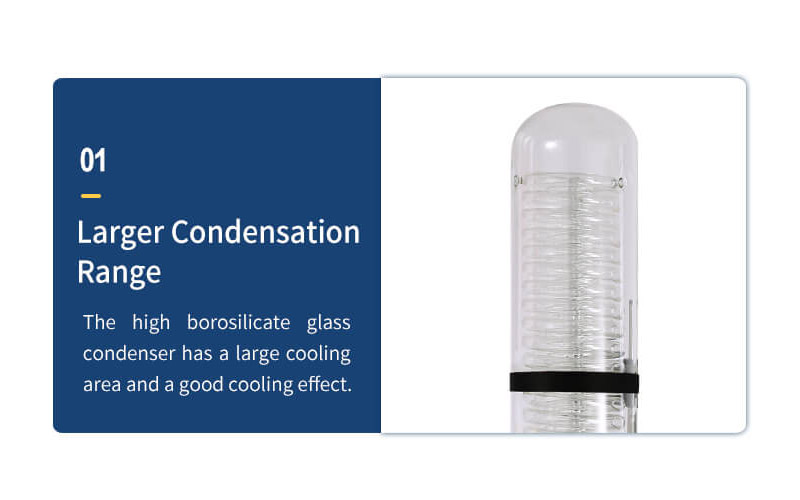
3. Utilizing Parallel Evaporation Systems:
Parallel evaporation systems complement rotovap machines by providing additional capacity for solvent removal. These systems consist of multiple heating blocks equipped with individual sample holders or microplates. Samples placed in the holders are simultaneously evaporated under controlled conditions, allowing for high-throughput solvent removal. Parallel evaporation systems can be integrated with rotovap setups to increase overall solution capacity and throughput.
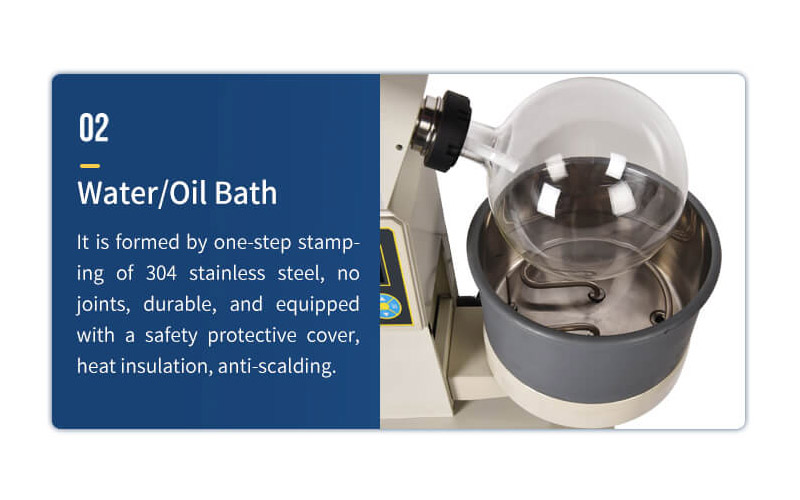
4. Exploring Automated Sample Handling:
Automation plays a vital role in increasing solution capacity and streamlining workflow processes in rotovap operations. Automated sample handling systems enable the automated introduction and removal of samples from the rotovap machine, reducing manual intervention and increasing throughput. Additionally, automated systems can perform repetitive tasks with precision and consistency, leading to improved efficiency and reproducibility.
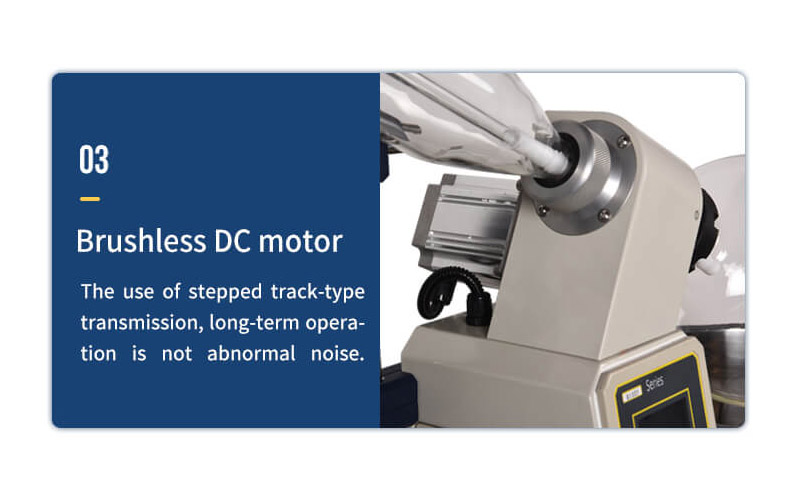
5. Optimizing Process Parameters:
Maximizing solution capacity also involves optimizing process parameters such as temperature, vacuum level, and rotation speed. Fine-tuning these parameters based on the characteristics of the solvent and sample can significantly impact evaporation efficiency and throughput. Experimentation and data analysis are essential for identifying optimal process conditions that balance solvent removal rates with sample integrity and quality.
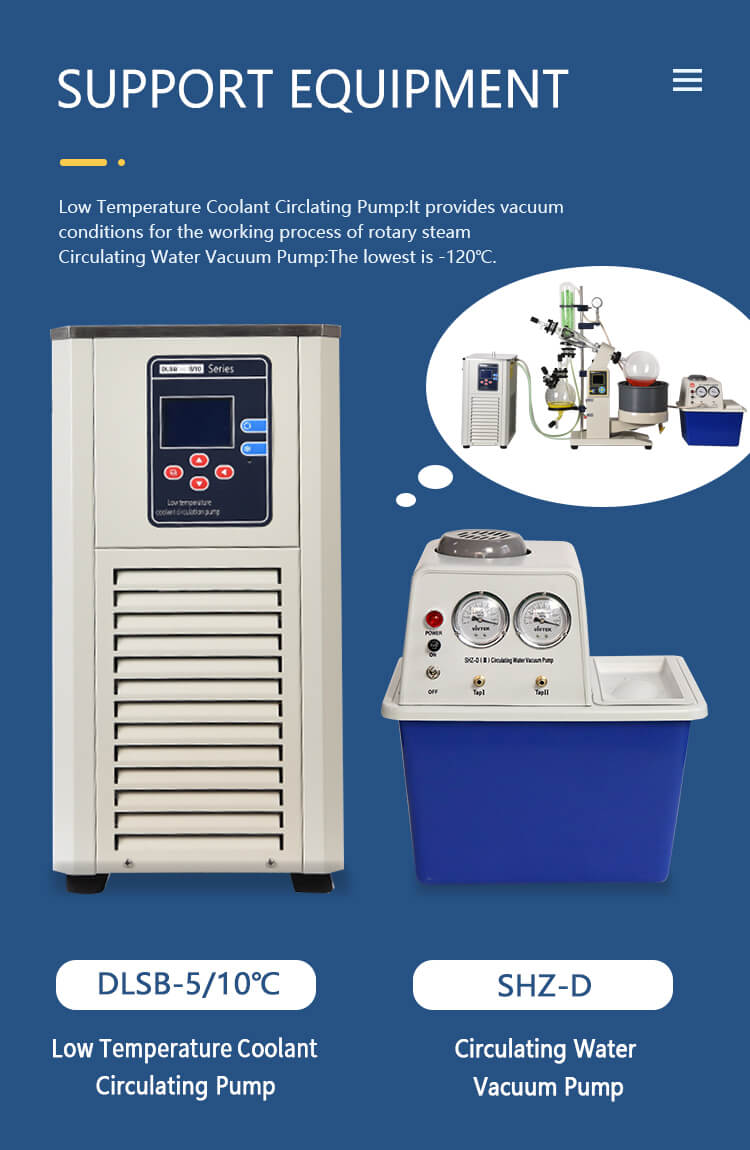
Expanding the solution capacity of rotovap machines is essential for meeting the demands of modern chemical and pharmaceutical applications. By implementing strategies such as upgrading to larger rotating flasks, implementing multi-flask systems, utilizing parallel evaporation systems, exploring automated sample handling, and optimizing process parameters, operators can enhance the efficiency and productivity of rotovap operations. As technology advances and industry demands evolve, staying informed about innovative solutions and best practices is key to maximizing the utility of rotovap machines in various applications. With a focus on increasing solution capacity and improving workflow efficiency, organizations can achieve greater success and productivity in their chemical and pharmaceutical endeavors.