What is a stainless steel reactor used for?
A stainless steel jacketed reactor is primarily used for carrying out chemical reactions on an industrial scale. Its robust construction and corrosion-resistant properties make it suitable for a wide range of applications in industries such as pharmaceuticals, chemicals, food processing, and more.
What are the advantages of using a stainless steel reactor?
Stainless steel reactors offer excellent corrosion resistance, durability, and thermal conductivity. They are easy to clean and maintain, making them ideal for processes that involve stringent hygiene standards. Additionally, stainless steel is non-reactive with most chemicals, ensuring the integrity of the reaction being carried out.
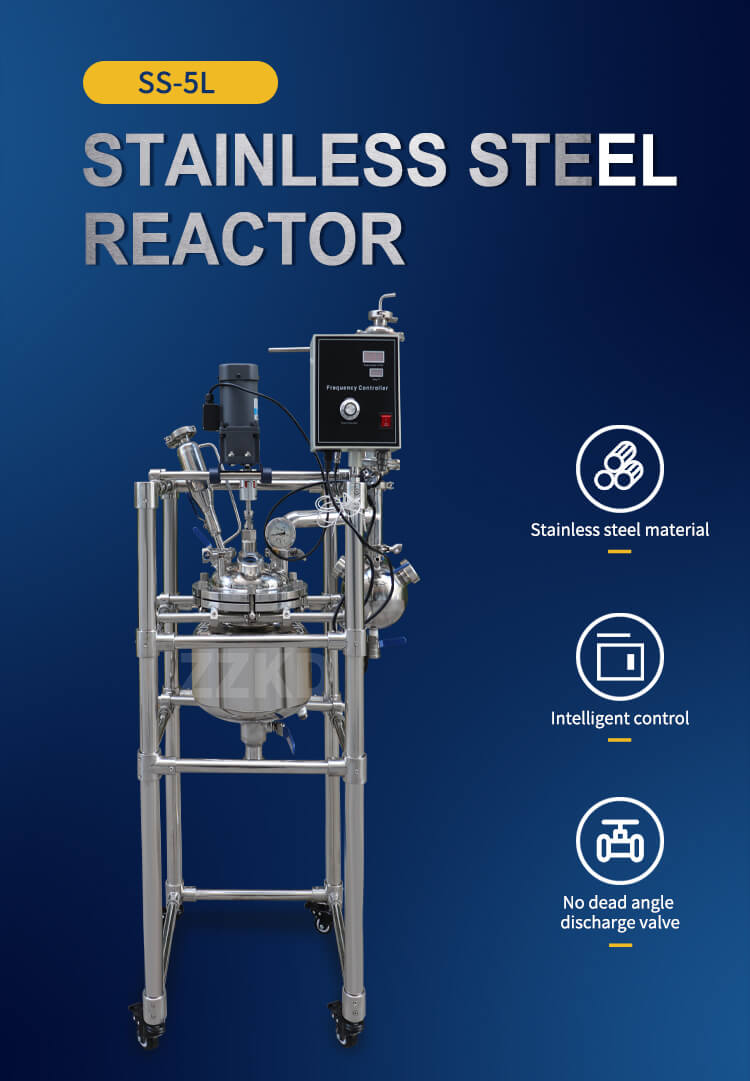
How do you choose the right size of a stainless steel reactor for a specific application?
The size of the stainless steel reactor should be chosen based on factors such as the volume of reactants, desired reaction conditions, and space constraints. It's essential to consider the batch size and scalability of the process to ensure efficient production.
What types of agitation mechanisms are available for stainless steel reactors?
Stainless steel reactors can be equipped with various agitation mechanisms, including paddle agitators, turbine agitators, and magnetic stirrers. The choice of agitation mechanism depends on factors such as the viscosity of the reaction mixture, mixing speed requirements, and the nature of the reaction being carried out.
Can stainless steel reactors withstand high temperatures and pressures?
Yes, stainless steel reactors are designed to withstand high temperatures and pressures, making them suitable for a wide range of reaction conditions. However, it's essential to ensure that the kettle is operated within its specified temperature and pressure limits to prevent any safety hazards.
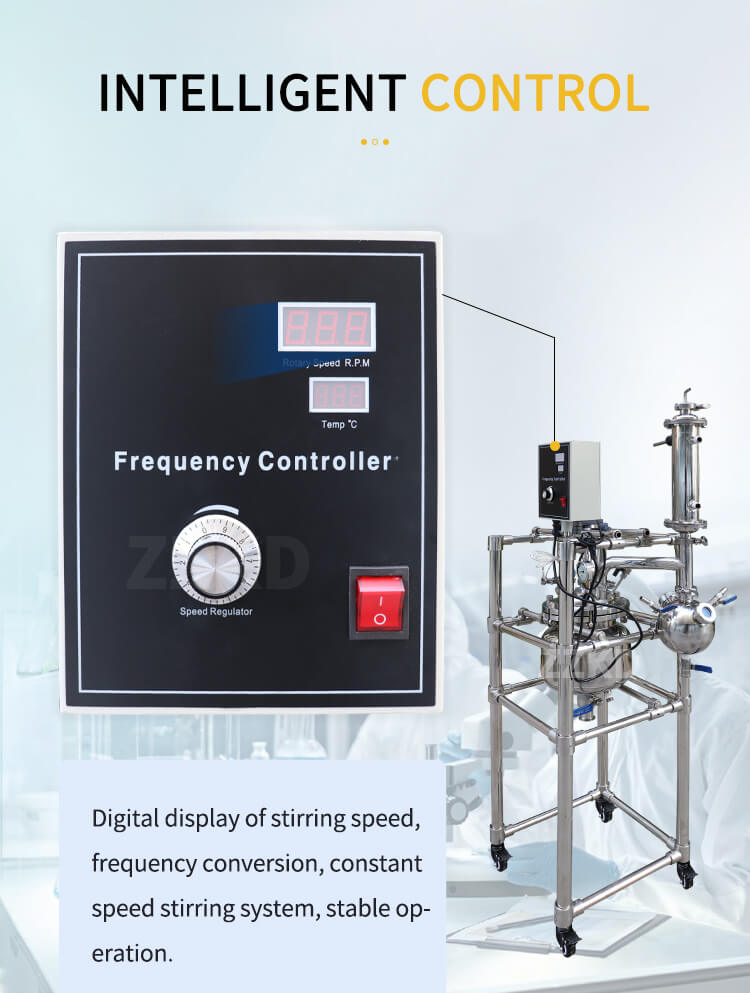
What safety features should be considered when operating a stainless steel reactor?
Safety features such as pressure relief valves, temperature sensors, and emergency shut-off systems should be installed to prevent overpressure and overheating situations. Additionally, proper ventilation and protective gear should be used when handling hazardous chemicals to minimize exposure risks.
How do you clean and maintain a stainless steel reactor?
SS reactor should be cleaned regularly using appropriate cleaning agents and procedures to remove any residues or contaminants. Routine maintenance tasks such as checking for leaks, inspecting agitators, and lubricating moving parts should also be performed to ensure optimal performance and longevity.
Are there any specific regulatory standards that stainless steel reactors need to comply with?
Stainless steel reactors used in industries such as pharmaceuticals and food processing must comply with relevant regulatory standards such as cGMP (current Good Manufacturing Practice) and FDA (Food and Drug Administration) regulations to ensure product safety and quality.
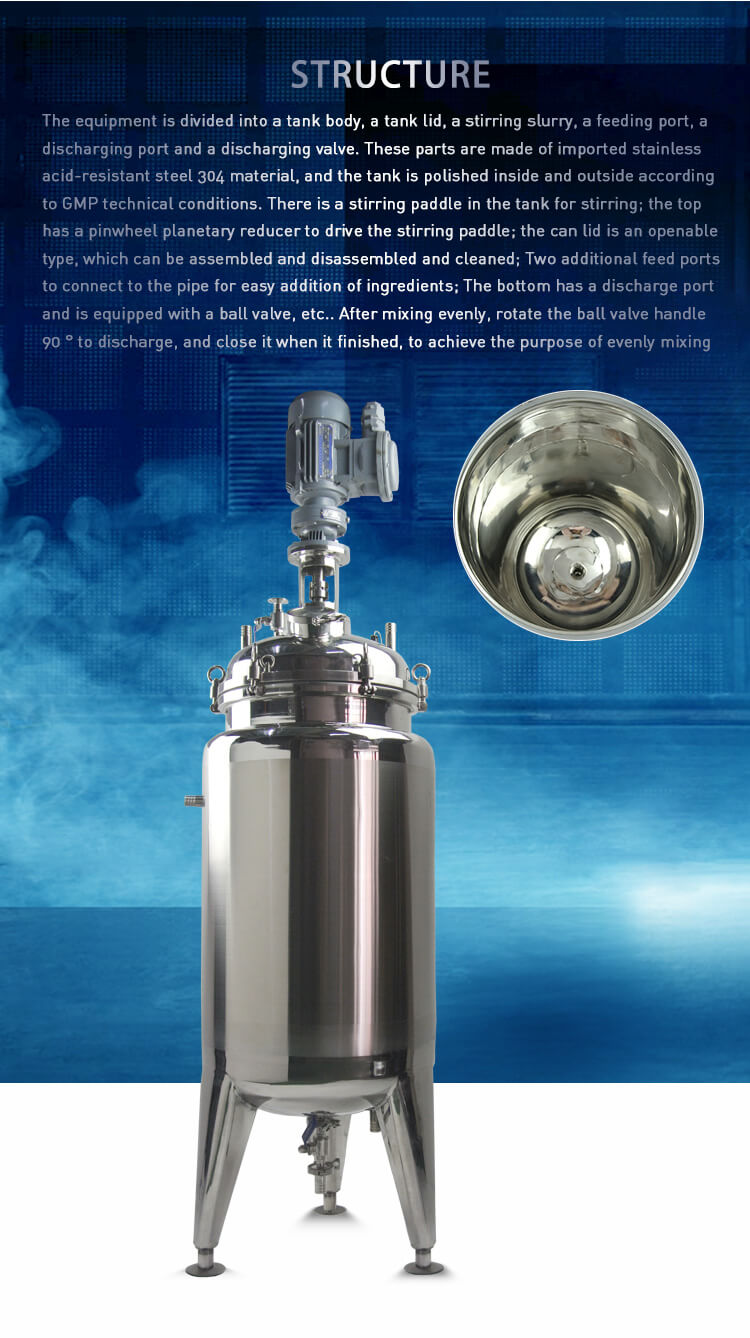
Can stainless steel reactors be customized to meet specific process requirements?
Yes, stainless steel reactors can be customized with features such as additional ports, baffles, insulation, and control systems to meet specific process requirements and accommodate various reaction parameters.
What materials can be processed in a stainless steel reactor?
Stainless steel reactors can be used to process a wide range of materials, including liquids, solids, and slurries. Common materials include chemicals, pharmaceutical ingredients, food products, polymers, and more.
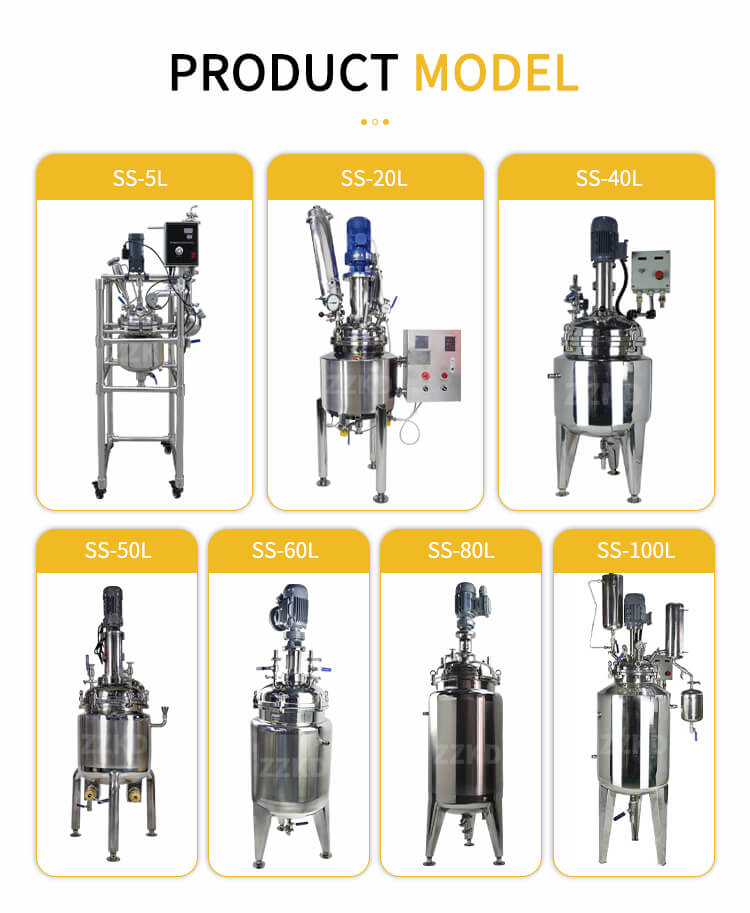
How do you ensure efficient heat transfer in a stainless steel reactor?
Efficient heat transfer in a stainless steel reactor can be ensured by using heating or cooling jackets, internal coils, or external heat exchangers. Proper agitation and circulation of the reaction mixture also help distribute heat evenly throughout the vessel.
What precautions should be taken when handling corrosive substances in a stainless steel reactor?
When handling corrosive substances, it's essential to use appropriate protective equipment such as gloves, goggles, and aprons to prevent skin and eye contact. stainless steel reactors should be resistant to corrosion, but care should still be taken to avoid prolonged exposure to corrosive chemicals.
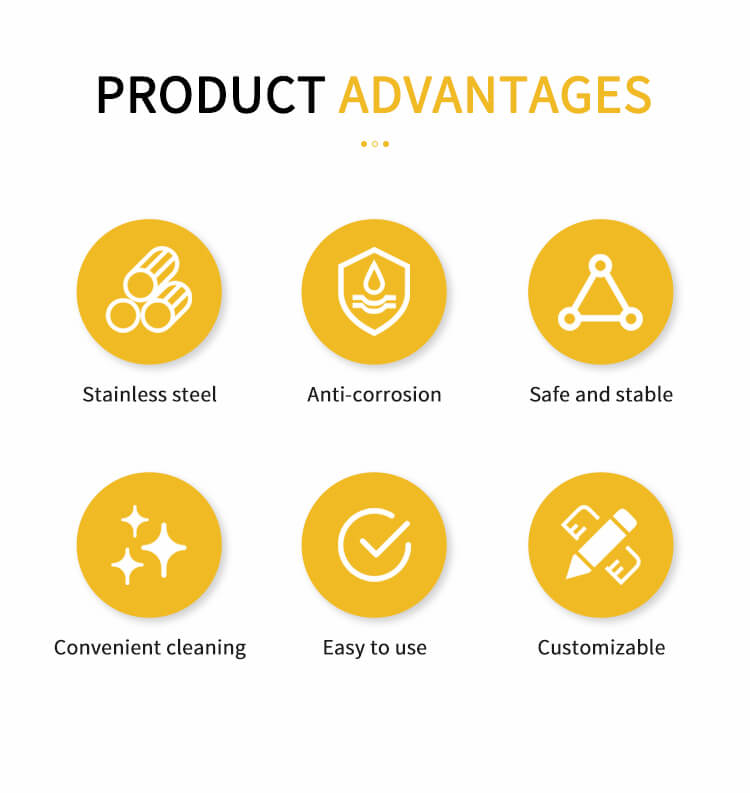
Can stainless steel reactors be used for batch or continuous processes?
Stainless steel reactor can be used for both batch and continuous processes, depending on the nature of the reaction and production requirements. Batch processes involve charging the kettle with reactants, carrying out the reaction, and then discharging the product, while continuous processes involve a continuous flow of reactants and products.
What factors affect the mixing efficiency of a stainless steel reactor?
Factors such as agitator design, mixing speed, viscosity of the reaction mixture, and baffling arrangements can affect the mixing efficiency of a stainless steel reactor. Proper optimization of these parameters is essential to ensure thorough mixing and homogeneity of the reaction mixture.
Are there any limitations to the types of reactions that can be carried out in a stainless steel reactor?
While stainless steel reactors are versatile and can accommodate a wide range of reactions, certain limitations may exist based on factors such as reaction kinetics, temperature and pressure requirements, and compatibility with materials of construction. It's essential to consider these factors when selecting a reaction vessel for a specific process.
What measures should be taken to prevent contamination in a stainless steel reactor?
To prevent contamination, stainless steel reactors should be cleaned thoroughly between batches, and proper hygiene practices should be followed during operation. Additionally, the use of dedicated equipment and segregation of incompatible materials can help minimize the risk of contamination.
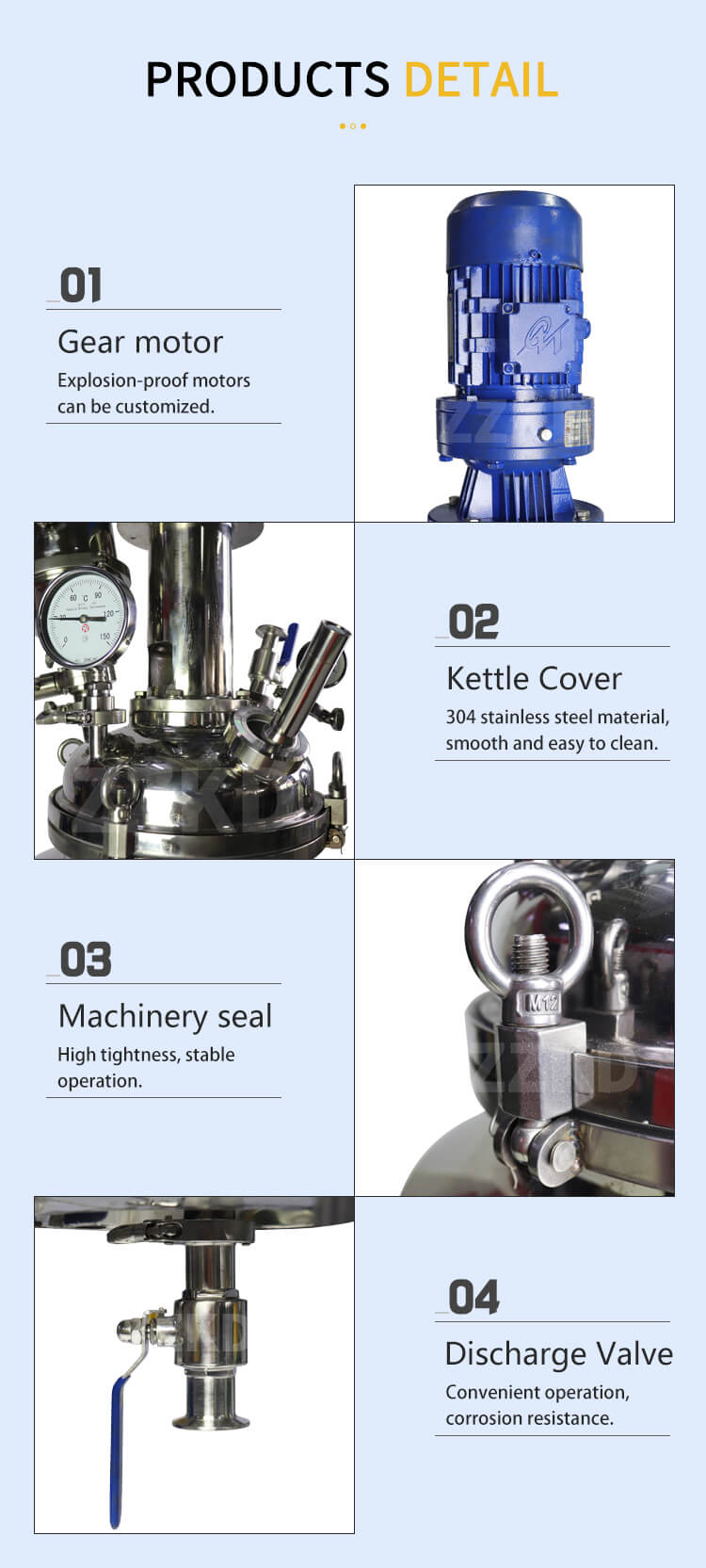
Can stainless steel reactors be used for reactions involving highly reactive or explosive substances?
Stainless steel reactors can be used for reactions involving highly reactive or explosive substances, provided that appropriate safety measures and containment systems are in place to mitigate the risks associated with such reactions.
What are some common troubleshooting issues encountered when operating a stainless steel reactor?
Common troubleshooting issues include leaks, agitator malfunctions, temperature fluctuations, and process upsets. These issues can often be resolved through routine maintenance, equipment inspections, and proper operator training.
How do you ensure proper venting and pressure control in a stainless steel reactor?
Proper venting and pressure control in a stainless steel reactor can be achieved by installing pressure relief valves, rupture discs, and venting systems designed to safely release excess pressure and prevent overpressurization of the vessel.
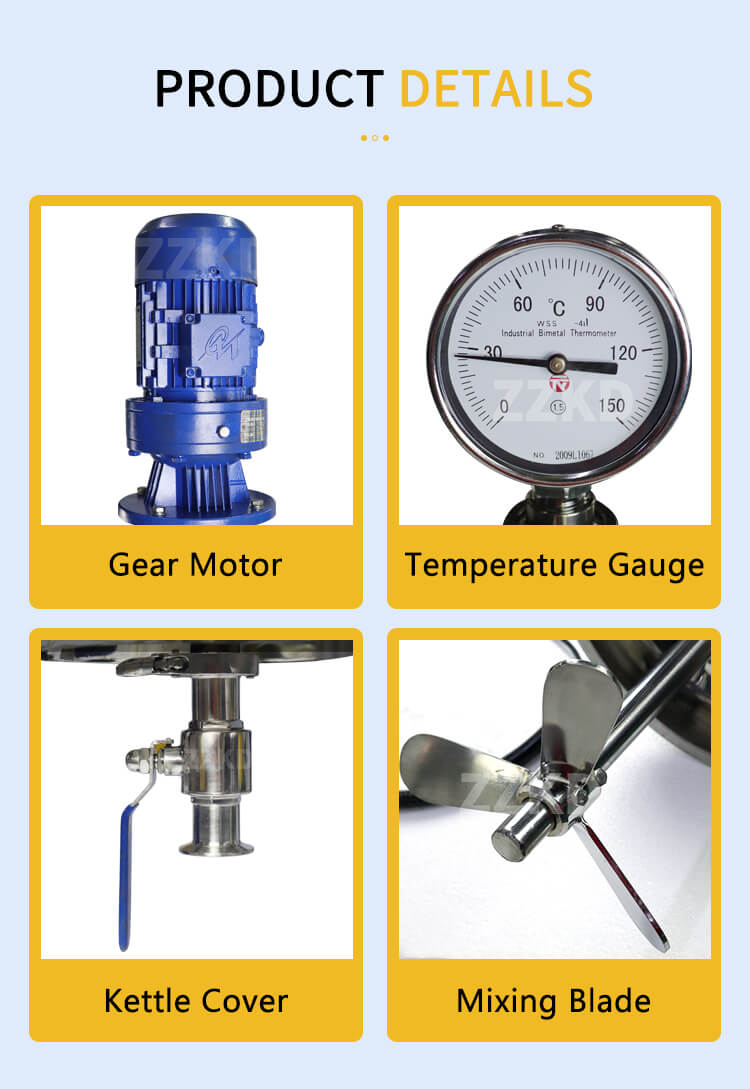
What are the environmental considerations associated with using stainless steel reactors?
Stainless steel reactors are generally considered environmentally friendly due to their durability, recyclability, and resistance to corrosion. However, proper waste management practices should be followed to dispose of any hazardous chemicals or by-products generated during the reaction process. Additionally, energy-efficient heating and cooling systems can help minimize environmental impact during operation.