What is a rotary evaporator?
A rotary evaporator is a laboratory instrument used to gently and efficiently remove solvents from samples by evaporation under reduced pressure and controlled temperature conditions. It consists of a rotating flask, a heating bath, a condenser, and a vacuum system. Rotary evaporators are widely used in organic chemistry laboratories for solvent removal, concentration, and purification.
How does a 1L rotary evaporator differ from larger models?
While the basic principles of operation remain the same across different sizes, the main difference lies in the volume capacity. A 1L rotavapor is smaller and suitable for processing smaller sample volumes compared to larger models like 2L, 5L, or higher capacities.
What are the advantages of using a 2L rotary evaporator?
A 2L rotary evaporator offers increased capacity compared to smaller models, allowing users to process larger sample volumes while still maintaining control over the evaporation process. It is suitable for applications requiring moderate sample sizes and provides more flexibility in experimental setups.
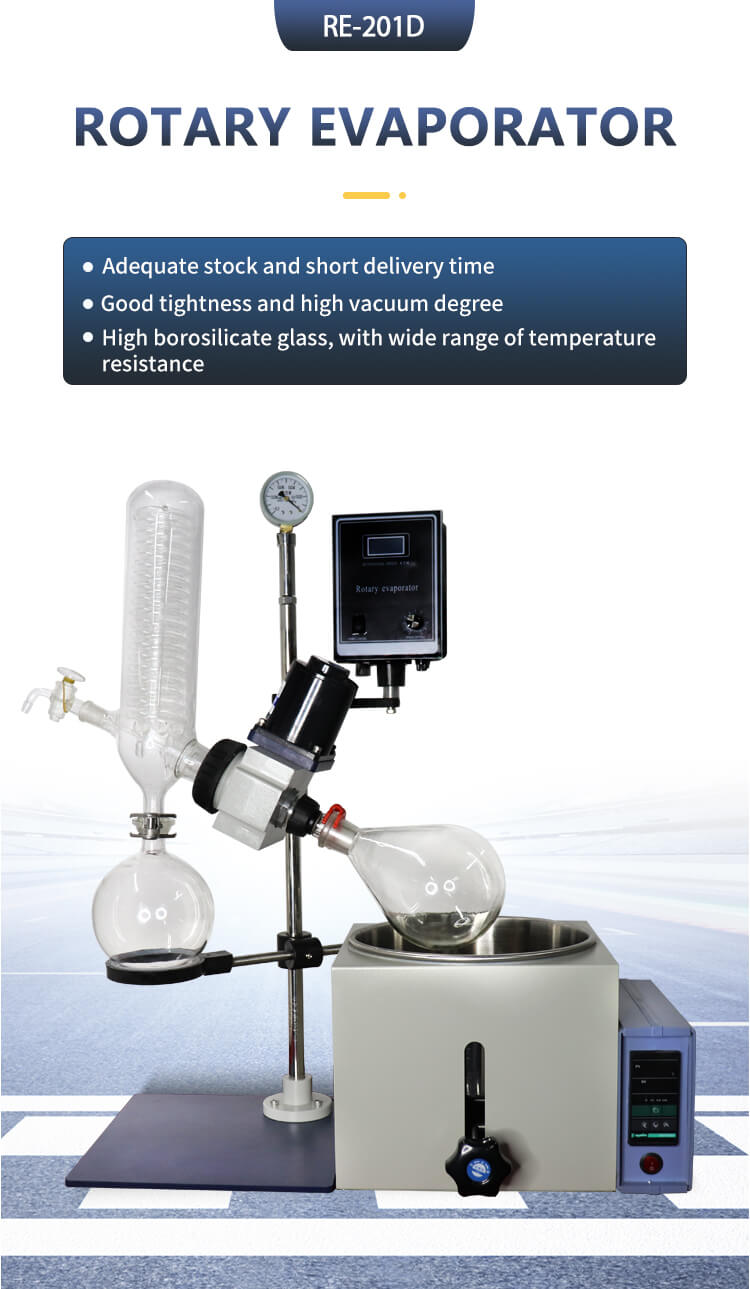
How can a 5L rotary evaporator benefit laboratory workflows?
With a larger volume capacity, a 5L rotary evaporator enables users to process larger batches of samples efficiently. This can be advantageous for laboratories with higher sample throughput requirements or when dealing with samples that require extended processing times.
What are the key features of a 10L rotavapor?
A 10L rotary evaporator offers even greater capacity, making it suitable for processing larger sample volumes or for scaling up experiments. It typically features robust construction, precise temperature control, and efficient solvent recovery capabilities, allowing for versatile applications in various laboratory settings.
How does a 20L rotary evaporator compare to smaller models?
A 20L rotary evaporator is designed for processing significantly larger sample volumes compared to smaller models. It provides enhanced productivity and throughput, making it ideal for laboratories with high sample demand or for applications requiring scale-up capabilities.
What considerations should be made when using a 50L rotary evaporator?
Operating a 50L rotavapor requires careful attention to safety protocols and equipment handling due to its larger size and higher capacity. Users should ensure proper ventilation, adequate space, and appropriate solvent handling procedures to optimize performance and minimize risks.
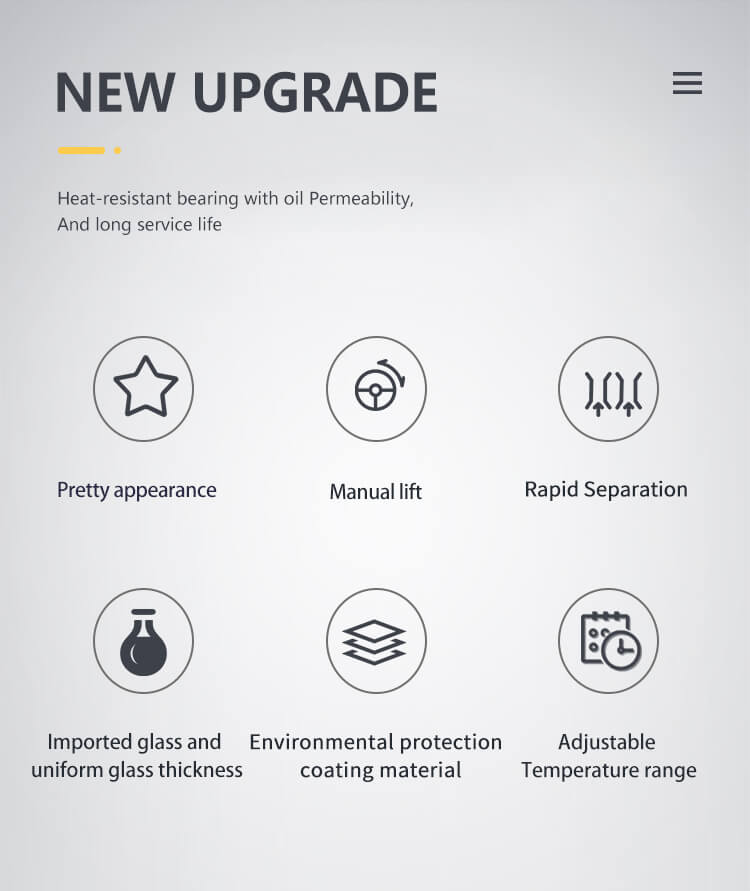
Can a 100L rotary evaporator handle highly volatile solvents?
Yes, a 100L rotary evaporator is capable of handling highly volatile solvents efficiently due to its robust design and advanced vapor management systems. However, proper safety precautions must be observed to prevent solvent leaks or other hazards associated with handling volatile substances at larger scales.
What are the typical applications of a 1L rotary evaporator in organic synthesis?
In organic synthesis, a 1L rotavapor is commonly used for solvent removal, concentration of reaction mixtures, and purification of compounds. It facilitates processes such as solvent exchange, drying of extracts, and isolation of product fractions, contributing to streamlined synthetic workflows.
How can a 2L rotary evaporator aid in natural product extraction?
For natural product extraction, a 2L rotary evaporator provides precise control over evaporation parameters, allowing researchers to optimize extraction conditions and maximize compound yields. It enables efficient removal of solvents from crude extracts while preserving the integrity of sensitive bioactive compounds.
What are the advantages of using a 5L rotary evaporator for pharmaceutical applications?
In pharmaceutical applications, a 5L rotary evaporator offers scalable solvent removal solutions for drug discovery, development, and formulation processes. It enables rapid concentration of active pharmaceutical ingredients (APIs) from reaction mixtures or plant extracts, facilitating downstream purification and characterization studies.
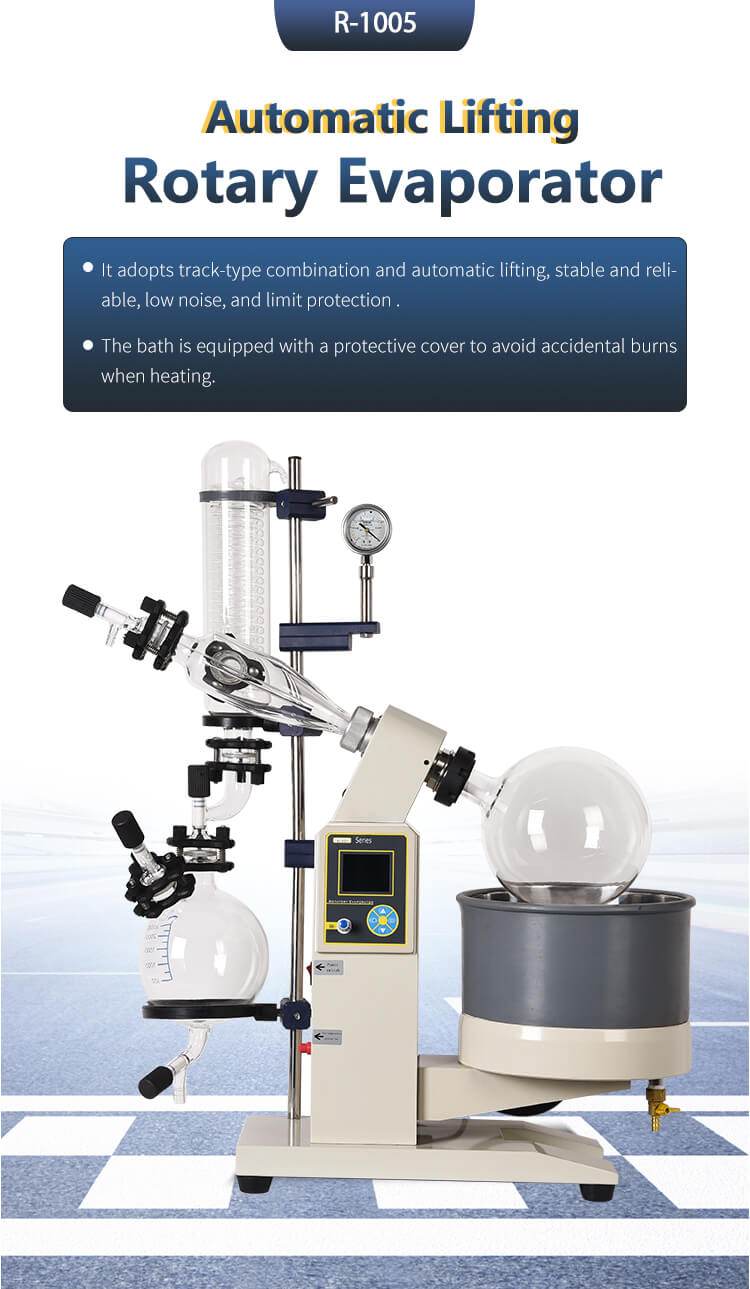
How does a 10L rotavapor contribute to medicinal chemistry research?
In medicinal chemistry research, a 10L rotary evaporator plays a crucial role in compound synthesis, purification, and analysis. It enables efficient removal of organic solvents from reaction mixtures, allowing researchers to isolate and characterize novel drug candidates with high purity and yield.
What factors should be considered when selecting a 20L rotary evaporator for industrial applications?
When choosing a 20L rotary evaporator for industrial use, factors such as solvent compatibility, throughput requirements, and ease of maintenance should be carefully evaluated. It is essential to select a model with robust construction, reliable performance, and customizable features to meet specific application demands and regulatory standards.
How can a 50L rotavapor enhance productivity in chemical process development?
In chemical process development, a 50L rotary evaporator enables efficient solvent removal and concentration of reaction intermediates, accelerating the optimization of synthetic routes and scale-up processes. It facilitates rapid evaluation of reaction parameters and provides valuable insights into reaction kinetics and thermodynamics.
What safety precautions should be followed when operating a 100L rotary evaporator in a pilot plant?
When using a 100L rotary evaporator in a pilot plant setting, strict adherence to safety protocols is paramount. This includes conducting risk assessments, implementing engineering controls, and providing comprehensive training to personnel involved in equipment operation and maintenance. Additionally, appropriate personal protective equipment (PPE) should be worn, and emergency procedures should be established to mitigate potential hazards and ensure a safe working environment.
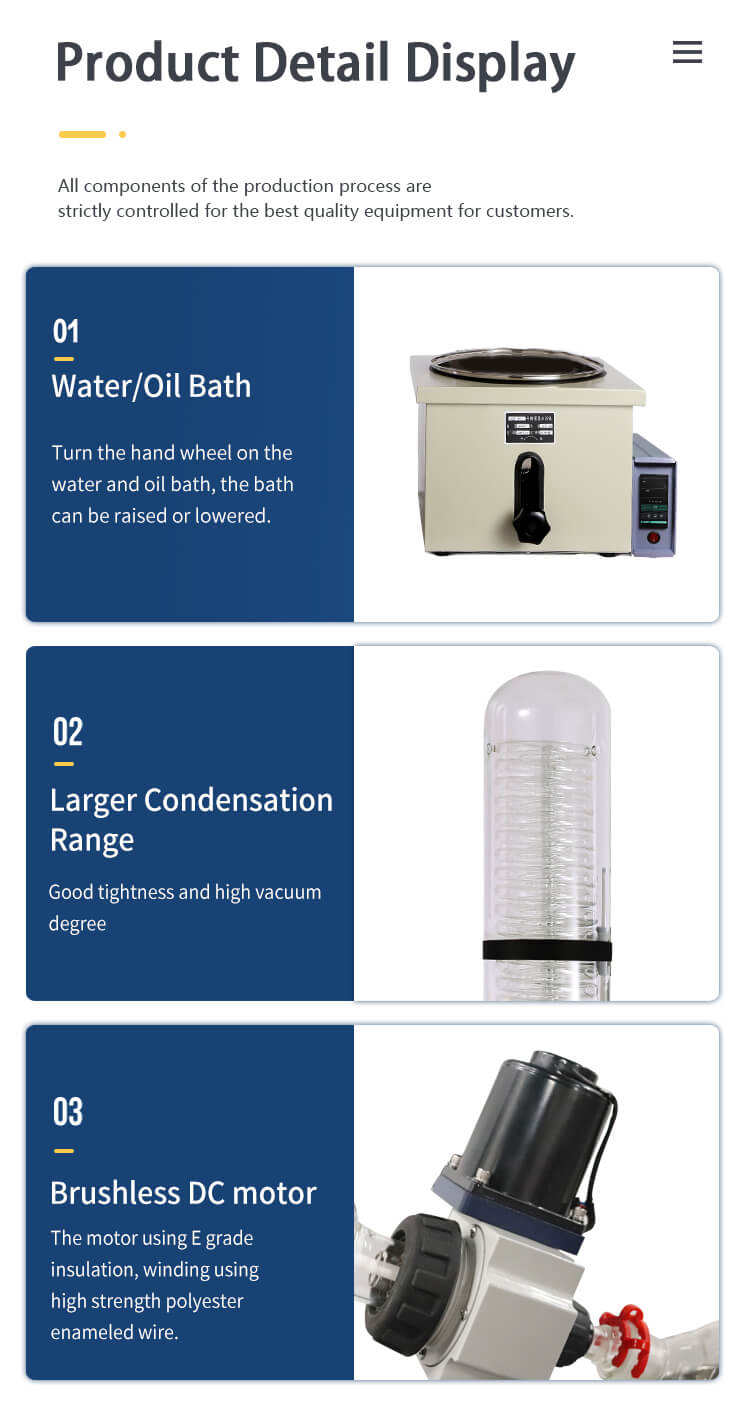
What are the primary components of a rotavapor and their functions?
A rotary evaporator typically consists of several key components, including a rotating flask, a heating bath or water bath, a condenser, a vacuum pump, and a collection flask. The rotating flask holds the sample to be evaporated, while the heating bath provides controlled heating to facilitate solvent evaporation. The condenser cools the evaporated solvent vapor, causing it to condense back into liquid form, which is then collected in the receiving flask. The vacuum pump creates a reduced pressure environment within the system, aiding in the evaporation process by lowering the boiling point of the solvent.
How does the rotation speed of the flask affect evaporation efficiency in a rotary evaporator?
The rotation speed of the flask in a rotary evaporator influences the surface area exposed to the heating bath, thereby affecting the rate of solvent evaporation. Higher rotation speeds can increase the evaporation rate by promoting better mixing of the sample and enhancing heat transfer between the liquid and vapor phases. However, excessively high rotation speeds may lead to splashing or foaming of the sample, necessitating careful adjustment to achieve optimal evaporation efficiency without compromising sample integrity.
Can a rotavapor be used for solvent recycling?
Yes, a rotary evaporator is commonly employed for solvent recycling and recovery purposes in laboratory and industrial settings. By subjecting solvent-containing mixtures to controlled evaporation under vacuum, the rotary evaporator enables the separation of solvents from non-volatile components, allowing for the recovery and reuse of valuable solvents while reducing waste and operating costs.
What precautions should be taken when handling volatile or flammable solvents with a rotary evaporator?
When working with volatile or flammable solvents, it is essential to observe strict safety protocols to prevent fire hazards and ensure operator safety. This includes performing solvent evaporation in a well-ventilated area with adequate ventilation and explosion-proof equipment. Additionally, users should avoid overheating and maintain proper vacuum levels to minimize the risk of solvent ignition or explosion. Proper containment and disposal procedures should also be followed to prevent environmental contamination and health risks.
How does the choice of condenser type impact the efficiency of solvent recovery in a rotavapor?
The selection of condenser type, such as a standard condenser or a cold trap condenser, can significantly influence the efficiency of solvent recovery in a rotary evaporator. A cold trap condenser, for example, is particularly effective for trapping volatile solvents and preventing them from contaminating the vacuum pump or escaping into the environment. By condensing solvent vapors at lower temperatures, cold trap condensers facilitate more efficient solvent recovery and enhance overall system performance.
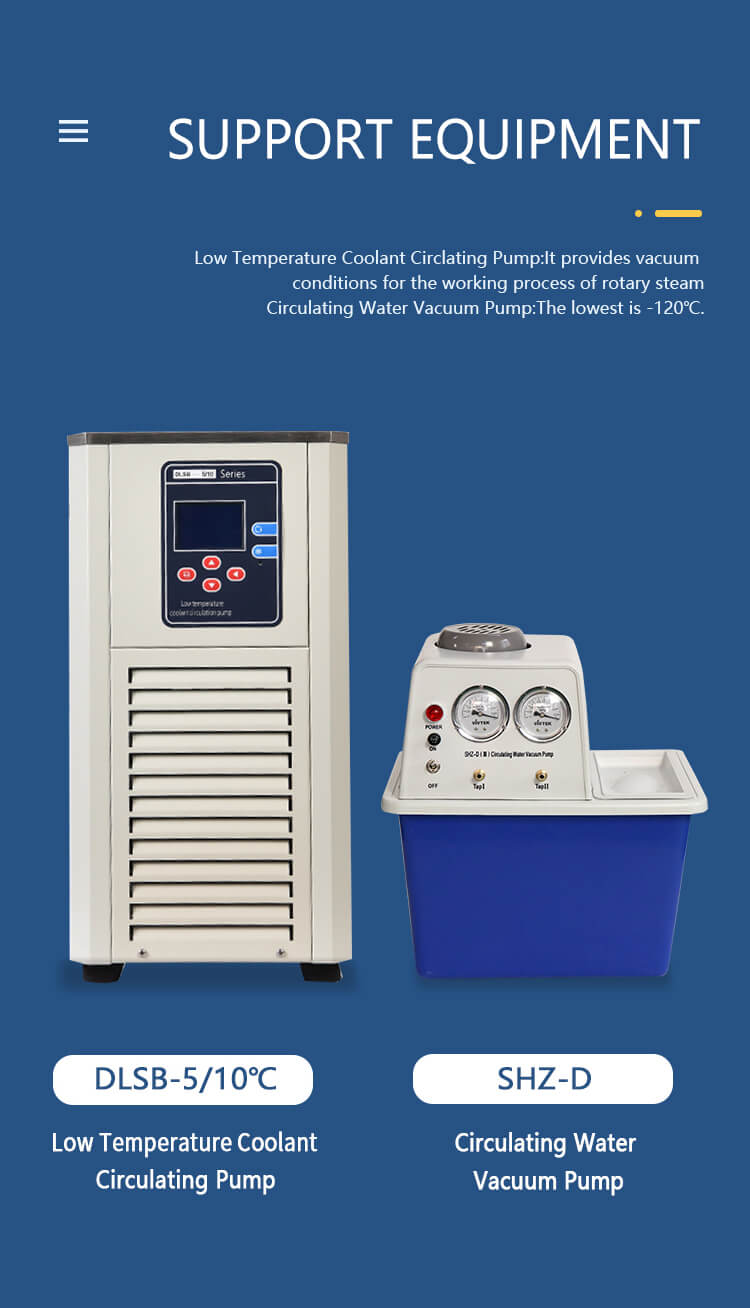
What are the benefits of using a rotavapor with a digital display and automated controls?
Rotary evaporators equipped with digital displays and automated controls offer several advantages, including enhanced precision, convenience, and reproducibility of experimental parameters. Users can easily monitor and adjust key parameters such as temperature, rotation speed, and vacuum levels, minimizing manual errors and ensuring consistent results across experiments. Additionally, built-in safety features and alarms help prevent operational errors and ensure optimal performance while streamlining workflow processes.
Can a rotary evaporator be used for concentration of heat-sensitive compounds?
Yes, a rotavapor is well-suited for the concentration of heat-sensitive compounds due to its ability to operate under reduced pressure and controlled temperature conditions. By evaporating solvents at lower temperatures, the risk of thermal degradation or decomposition of sensitive compounds is minimized, allowing for the efficient concentration and isolation of heat-labile substances while preserving their chemical integrity and biological activity.
What are the factors to consider when selecting a vacuum pump for use with a rotary evaporator?
When choosing a vacuum pump for a rotary evaporator, factors such as pumping speed, ultimate vacuum level, chemical compatibility, noise level, and maintenance requirements should be taken into account. The vacuum pump should be capable of achieving and maintaining the desired vacuum level to facilitate efficient solvent evaporation while withstanding exposure to corrosive or reactive vapors commonly encountered during solvent removal processes.
How can solvent bumping be prevented during rotary evaporation?
Solvent bumping, or sudden boiling and ejection of solvent from the flask, can be prevented by employing several strategies, including the use of anti-bumping granules or boiling chips, maintaining a gentle rotation speed, and ensuring proper flask loading to promote even heat distribution. Additionally, adjusting the vacuum level and controlling the heating rate can help minimize the occurrence of solvent bumping while optimizing evaporation efficiency and sample integrity.
What are the limitations of using a rotavapor for solvent removal?
While rotary evaporators are highly versatile and efficient for solvent removal in many applications, they may have limitations when dealing with certain types of samples or solvents. For instance, viscous or high-boiling-point solvents may require longer evaporation times or specialized equipment configurations to achieve complete solvent removal. Similarly, samples containing volatile components or complex matrices may present challenges in terms of solvent recovery efficiency and process optimization.
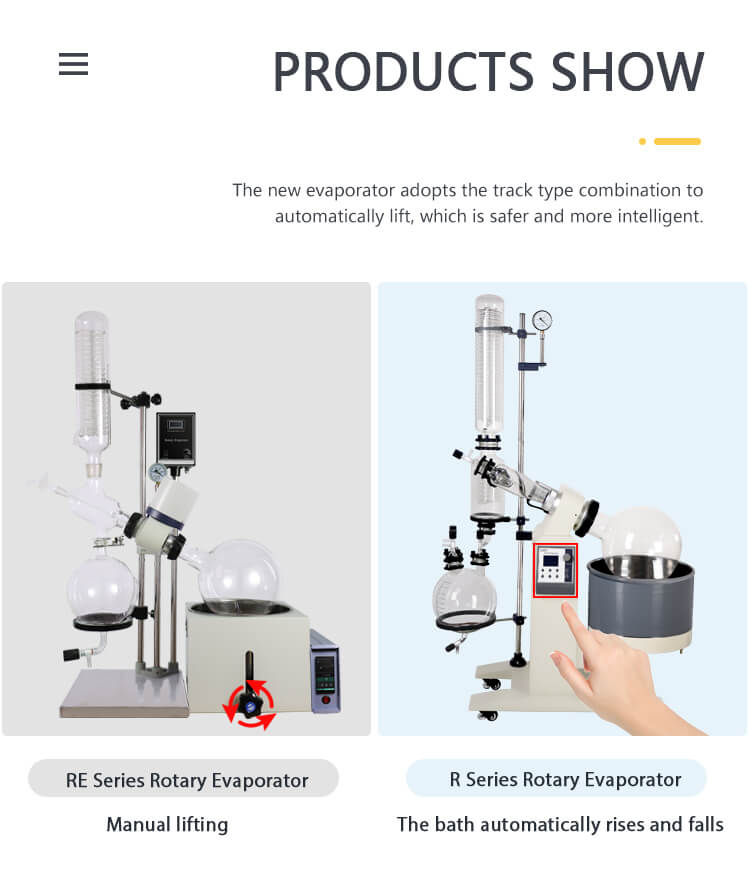
How can sample contamination be minimized during rotary evaporation?
To minimize sample contamination during rotary evaporation, it is essential to ensure the cleanliness of all system components, including glassware, condensers, and vacuum lines. Proper solvent purification and filtration techniques should be employed to remove impurities and particulate matter that may compromise sample purity. Additionally, conducting solvent blank runs and implementing stringent laboratory practices, such as avoiding cross-contamination and using dedicated equipment for specific applications, can help maintain sample integrity and reproducibility.
What maintenance procedures are recommended for ensuring the longevity and optimal performance of a rotary evaporator?
Routine maintenance procedures for rotavapors may include cleaning and sterilization of glassware, inspection and replacement of worn or damaged seals, lubrication of moving parts, calibration of temperature and vacuum gauges, and periodic testing of safety features and emergency shut-off mechanisms. Regular preventative maintenance helps identify potential issues early and ensures reliable operation while minimizing downtime and costly repairs.
Can a rotavapor be used for solvent extraction from solid samples?
Yes, a rotary evaporator can be used for solvent extraction from solid samples by suspending the sample in a suitable solvent and subjecting it to controlled evaporation under vacuum. The solvent extracts the desired components from the solid matrix, and the evaporator facilitates solvent removal, leaving behind the concentrated extract for further analysis or processing. This method is commonly employed in analytical chemistry, environmental testing, and natural product isolation procedures.
What are the environmental and economic benefits of solvent recovery using a rotary evaporator?
Solvent recovery using a rotary evaporator offers significant environmental and economic benefits by reducing solvent consumption, minimizing waste generation, and lowering operating costs associated with solvent procurement and disposal. By recycling and reusing solvent resources, laboratories and industrial facilities can decrease their environmental footprint, conserve natural resources, and contribute to sustainable practices in chemical processing and manufacturing.
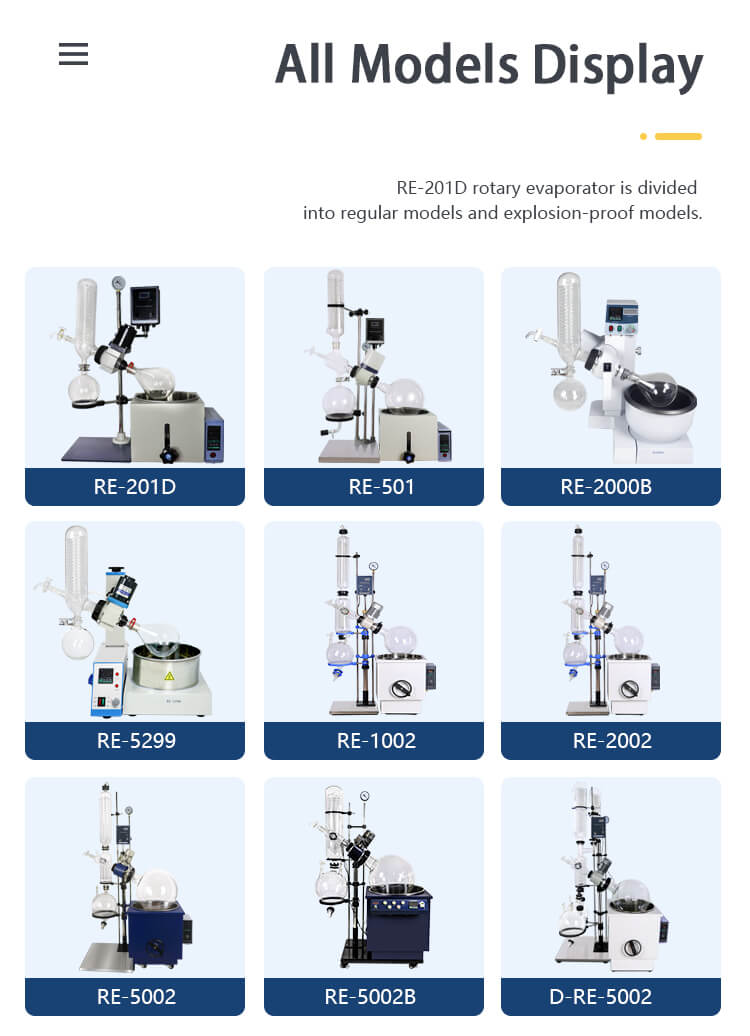
How does the scalability of rotary evaporators impact process development and production scale-up?
The scalability of rotavapors from smaller laboratory-scale units to larger industrial-scale systems provides valuable flexibility and continuity in process development and production scale-up activities. It allows researchers and engineers to optimize process parameters, evaluate equipment performance, and validate production protocols at various stages of development, ensuring seamless transition from bench-scale experimentation to full-scale manufacturing while minimizing risks and uncertainties.