In the world of chemical and pharmaceutical manufacturing, reactors play a crucial role in driving chemical reactions under controlled conditions. One of the most significant parameters that affect reactor performance is pressure. Higher pressure reactors are often required for various applications, especially when dealing with reactions involving gases or when aiming for faster reaction rates and higher yields. But what type of reactor can operate at higher pressures? This article delves into the details, exploring the characteristics, advantages, and applications of high pressure reactors.
Understanding High Pressure Reactors
High pressure reactors are designed to operate at pressures significantly higher than atmospheric pressure. These reactors are engineered to withstand the stresses and strains associated with high pressure environments, ensuring safe and efficient operation. The materials used in their construction, the design features, and the safety mechanisms are all tailored to handle elevated pressures.
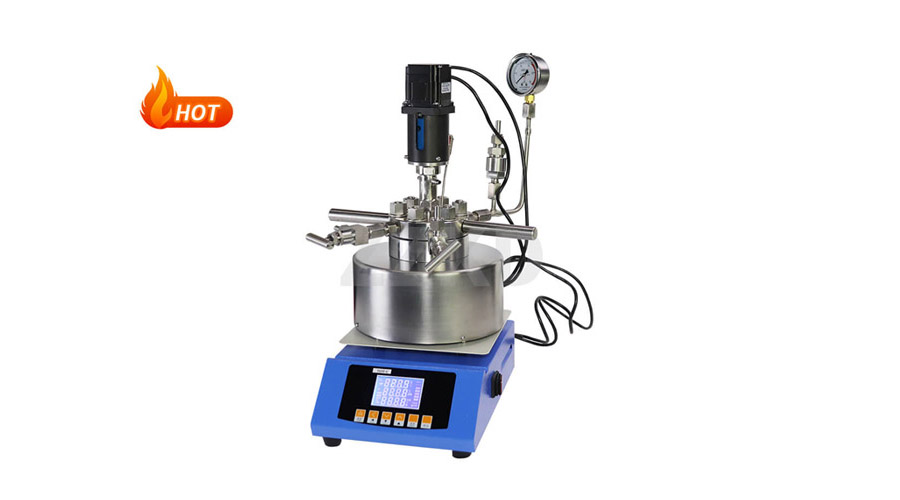
Key Types of High Pressure Reactors
There are several types of reactors capable of operating at high pressures, each suited to different applications and processes. Here are some of the most commonly used high pressure reactors:
-
High Pressure Autoclave Reactor
-
CSTRs (Continuous Stirred Tank Reactors)
-
Tubular Reactors
-
Hydrothermal Reactors
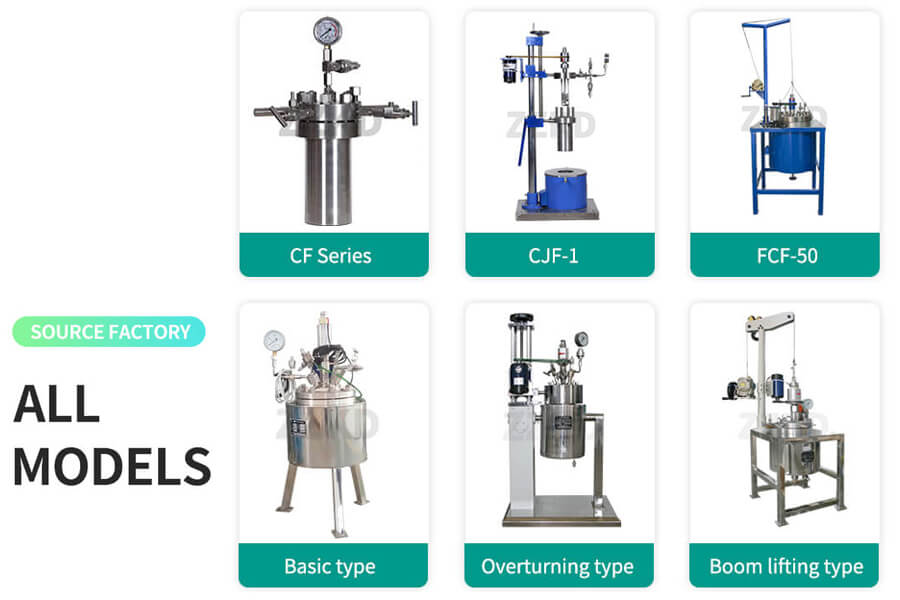
Each of these reactors has unique features and applications, making them suitable for various high pressure processes.
High Pressure Autoclave Reactor
High Pressure Autoclave Reactor are one of the most versatile types of high pressure reactors. They are used in a wide range of applications, from chemical synthesis to sterilization in the medical field. Autoclaves can maintain high pressures and temperatures, making them ideal for reactions that require such conditions.
Why are autoclaves preferred for high pressure applications in both chemical and medical fields?
High Pressure Autoclave Reactor are preferred because they can provide a controlled environment for both chemical reactions and sterilization processes. The ability to control temperature and pressure precisely ensures that reactions proceed efficiently and that sterilization is thorough.
Continuous Stirred Tank Reactors (CSTRs)
CSTRs are widely used in the chemical industry for continuous production processes. These reactors can be designed to operate at high pressures, making them suitable for reactions involving gases or volatile components. The continuous nature of CSTRs allows for a steady production rate, which is advantageous for industrial scale operations.
What makes CSTRs advantageous for industrial scale high pressure processes?
The continuous operation of CSTRs ensures a consistent output, which is critical for large scale production. Additionally, the ability to maintain high pressures allows for the use of gases as reactants, which can enhance reaction rates and yields.
Batch Reactors
Batch reactors are commonly used in laboratories and small scale production settings. These reactors can be designed to withstand high pressures, making them suitable for various research and development applications. Batch reactors offer flexibility in terms of reaction time and conditions, allowing for precise control over the process.
How does the flexibility of batch reactors benefit high pressure research and development?
The flexibility of batch reactors allows researchers to experiment with different reaction conditions and times, providing valuable insights into the behavior of reactions under high pressure conditions. This adaptability is essential for developing new processes and optimizing existing ones.
Hydrothermal Reactors
Hydrothermal reactors are specifically designed for reactions involving water at high temperatures and pressures. These reactors are commonly used in the synthesis of advanced materials, such as nanomaterials and zeolites. The high pressure environment in hydrothermal reactors promotes the dissolution and recrystallization of materials, leading to the formation of unique structures.
Hydrothermal reactors are ideal for applications that require the use of superheated water as a solvent. The high pressure environment facilitates the formation of complex materials with desirable properties.
Advantages of High Pressure Reactors
Operating at high pressures offers several advantages in chemical and pharmaceutical processes. Here are some of the key benefits:
-
Increased Reaction Rates: High pressure can increase the concentration of reactants, leading to faster reaction rates.
-
Higher Yields: Elevated pressures can drive reactions to completion, resulting in higher yields of the desired products.
-
Improved Selectivity: High pressure conditions can enhance the selectivity of certain reactions, reducing the formation of unwanted by products.
-
Enhanced Solubility: High pressures can improve the solubility of gases and solids in liquids, facilitating reactions that would be difficult under atmospheric conditions.
-
Versatility: High pressure reactors can be used for a wide range of applications, from chemical synthesis to material science and pharmaceutical production.
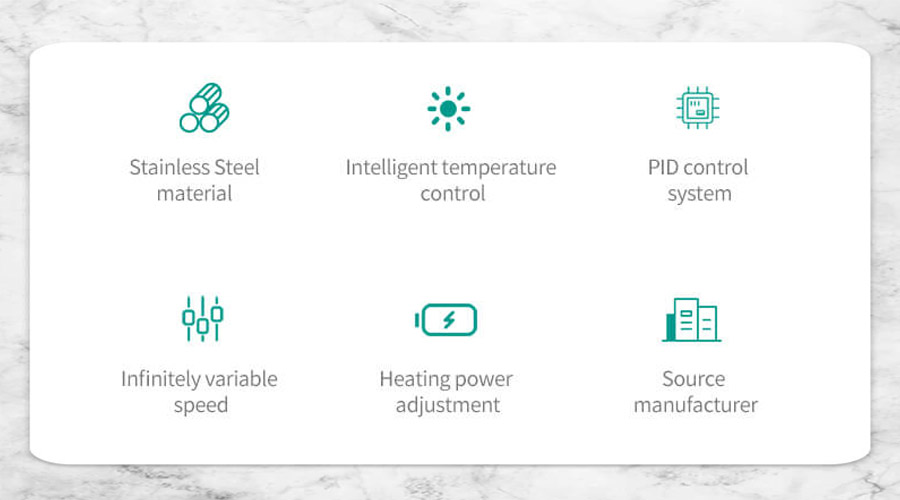
Applications of High Pressure Reactors
High pressure reactors are employed in various industries and applications due to their ability to handle demanding conditions. Some notable applications include:
-
Chemical Synthesis: High pressure reactors are used in the synthesis of chemicals and intermediates, where high pressures can improve reaction efficiency and yield.
-
Pharmaceutical Manufacturing: The pharmaceutical industry utilizes high pressure reactors for the production of active pharmaceutical ingredients (APIs) and other compounds.
-
Material Science: In material science, high pressure reactors are used for the synthesis of advanced materials, such as nanomaterials and polymers.
-
Petrochemical Industry: High pressure reactors are essential in the petrochemical industry for processes like hydrocracking and catalytic reforming.
-
Food and Beverage: The food and beverage industry uses high pressure reactors for processes such as pasteurization and sterilization.
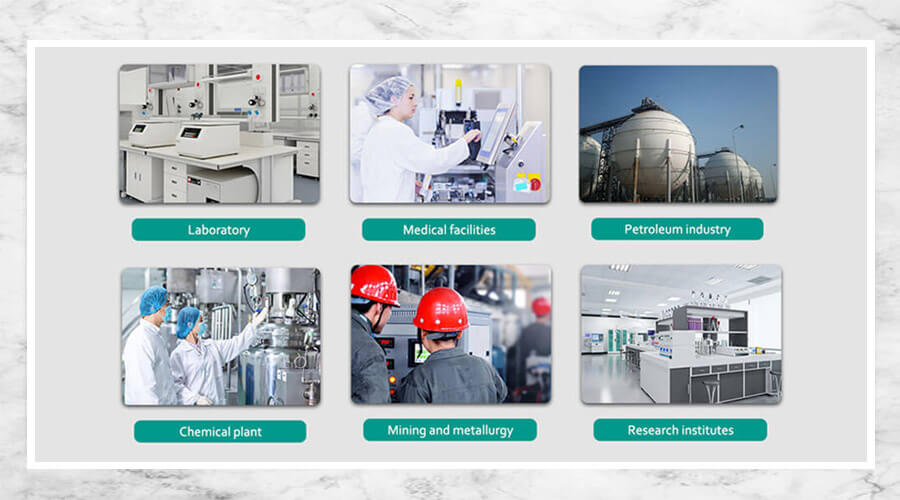
Safety Considerations
Operating at high pressures requires stringent safety measures to prevent accidents and ensure the integrity of the reactor. Here are some key safety considerations:
-
Material Selection: The materials used in high pressure reactors must be capable of withstanding the stresses associated with high pressure environments.
-
Pressure Relief Systems: High pressure reactors must be equipped with pressure relief systems to prevent overpressure situations.
-
Monitoring and Control: Continuous monitoring and control of pressure and temperature are essential to ensure safe operation.
-
Regular Maintenance: Regular maintenance and inspection of high pressure reactors are crucial to identify and address potential issues before they lead to failures.
-
Training and Procedures: Proper training for personnel and established operating procedures are vital for the safe handling of high pressure reactors.
Conclusion
High pressure reactors are indispensable in various industrial applications due to their ability to operate under demanding conditions. Whether it's for chemical synthesis, pharmaceutical manufacturing, or material science, the ability to maintain high pressures opens up new possibilities and enhances process efficiency. Understanding the different types of high pressure reactors and their advantages allows industries to select the most suitable equipment for their specific needs.
By considering the safety aspects and leveraging the benefits of high pressure reactors, industries can achieve higher yields, improved reaction rates, and enhanced product quality. The versatility and robustness of these reactors make them a valuable asset in advancing technology and innovation in numerous fields.
In conclusion, the choice of reactor for high pressure applications depends on the specific requirements of the process. Whether it's an autoclave for sterilization, a CSTR for continuous production, or a hydrothermal reactor for material synthesis, each type of reactor offers unique advantages. By carefully selecting and operating high pressure reactors, industries can unlock new potential and drive progress in their respective fields.