In the world of chemical and pharmaceutical industries, the choice of equipment can significantly impact the efficiency and outcomes of various processes. One such indispensable piece of equipment is the jacketed glass reactor. Known for its versatility, precision, and reliability, the jacketed glass reactor is a crucial asset in both research laboratories and industrial settings. But what makes this equipment so essential, and how can it benefit your operations? Let’s delve into the remarkable features and advantages of jacketed glass reactors.
What is a Jacketed Glass Reactor?
A jacketed glass reactor vessel is a vessel designed for conducting chemical reactions under controlled conditions. The key feature of this reactor is its double-layered construction. The inner layer holds the reactants, while the outer jacket allows the circulation of thermal fluids, which can be heated or cooled as needed. This design enables precise temperature control, which is vital for many chemical reactions.
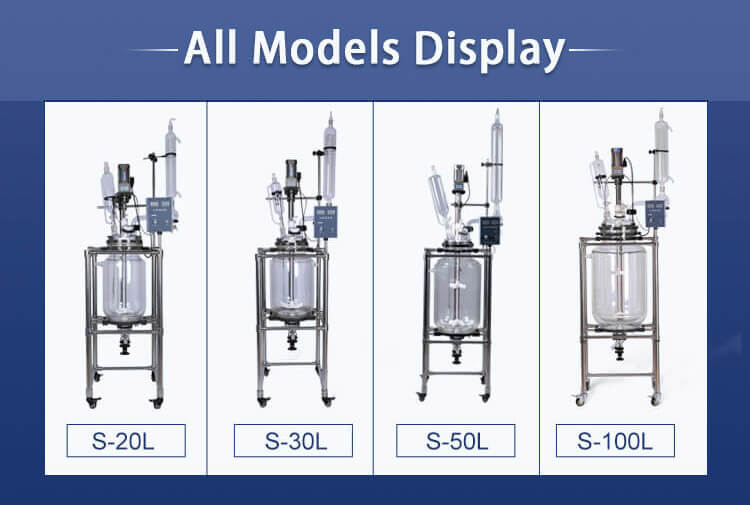
The Importance of Temperature Control
Why is temperature control so crucial in chemical reactions? Chemical reactions are highly sensitive to temperature changes. A slight deviation can result in incomplete reactions, undesired by-products, or even dangerous conditions. The jacketed glass reactor ensures that the reaction temperature is maintained within the desired range, thereby enhancing the reaction efficiency and safety.
For instance, in pharmaceutical synthesis, maintaining an exact temperature is essential to achieve the desired product purity and yield. Similarly, in chemical research, precise temperature control can mean the difference between success and failure in experiments. Have you ever faced challenges in achieving consistent reaction results? The answer might lie in the temperature control capabilities of your reactor.
Advantages of Using a Jacketed Glass Reactor
1. Versatility
Jacketed glass reactors are incredibly versatile and can be used for a wide range of applications. Whether it’s mixing, dissolving, crystallizing, or extracting, these reactors can handle it all. This versatility makes them ideal for research and development activities where various types of reactions are often performed.
2. Transparency
The glass construction of these reactors allows for easy visual monitoring of the reaction process. This transparency is particularly beneficial in research settings where observing the reaction progress is crucial. It helps in making timely adjustments to the process parameters, ensuring optimal results.
3. Material Compatibility
Glass is highly resistant to chemical corrosion, making jacketed glass reactors suitable for handling a wide range of chemicals, including highly corrosive ones. This compatibility extends the lifespan of the reactor and ensures that the quality of the reaction is not compromised by material degradation.
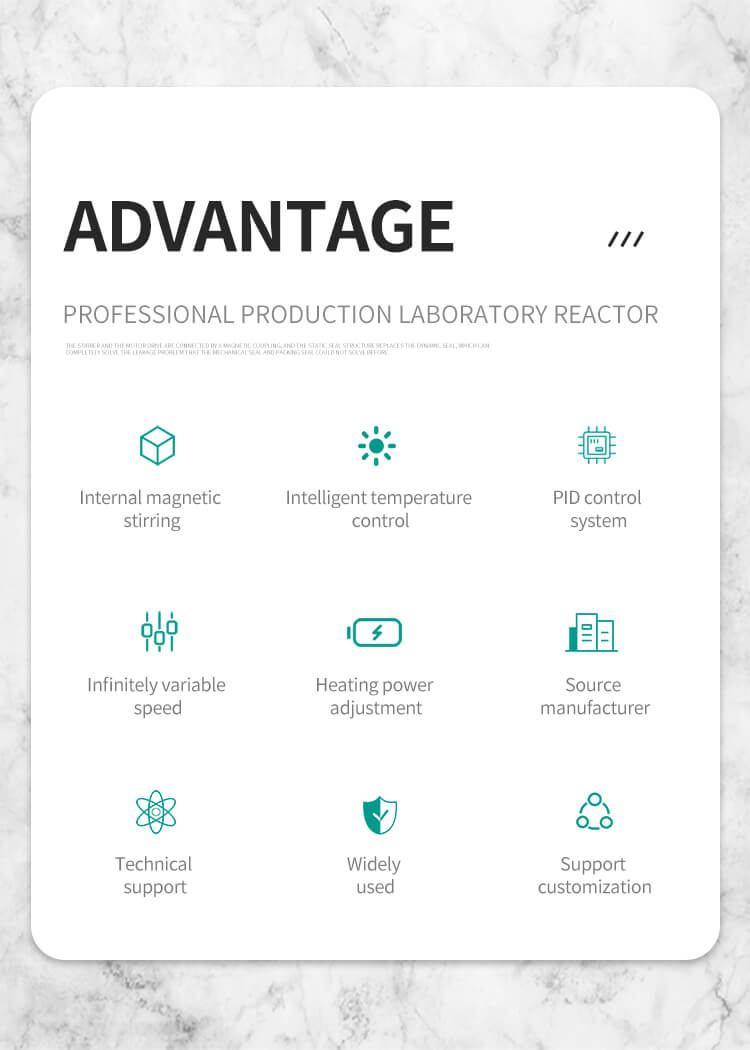
How Does a Jacketed Glass Reactor Enhance Safety?
Safety is a paramount concern in any chemical processing environment. The jacketed glass reactor enhances safety in several ways. Firstly, the jacketed design allows for indirect heating and cooling, reducing the risk of thermal shock and sudden temperature fluctuations. Secondly, the transparency of the glass provides an immediate visual cue if something goes wrong, such as a color change indicating an unwanted reaction. Lastly, these reactors are designed to withstand high pressures, adding an extra layer of safety when dealing with volatile reactions.
Customization and Scalability
Another significant advantage of jacketed glass reactors is their customization and scalability. They are available in various sizes, from small laboratory-scale models to large industrial reactors. This scalability allows businesses to start small and expand their operations without needing to invest in entirely new equipment.
Customization options include different types of glass (such as borosilicate for higher thermal resistance), various jacket configurations, and additional features like vacuum adapters and stirring mechanisms. This flexibility ensures that the reactor can be tailored to meet specific process requirements. Have you considered the specific needs of your operation and how a customized reactor could address them?
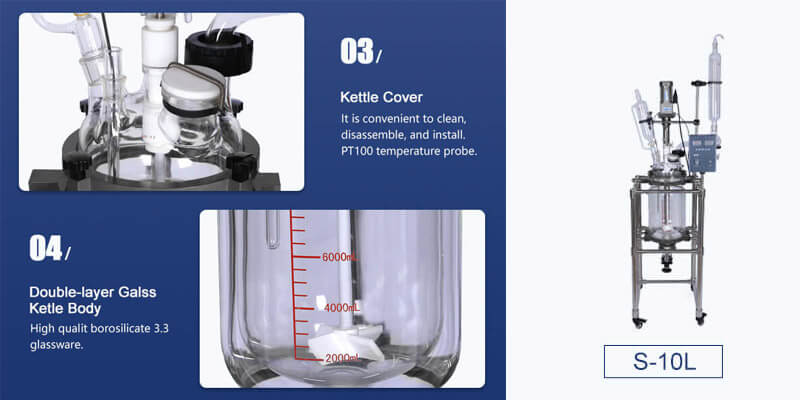
Efficient Mixing and Stirring
Efficient mixing is essential for uniform reaction conditions. Jacketed glass reactors often come with integrated stirring mechanisms that ensure thorough mixing of the reactants. This feature is particularly important for reactions involving solid particles or when a homogeneous mixture is required for optimal reaction performance.
Ease of Cleaning and Maintenance
Maintaining a clean reactor is crucial for preventing contamination between different batches of products. The smooth glass surface of jacketed reactors makes them easy to clean, ensuring that residues are easily removed. This ease of cleaning not only saves time but also enhances the reliability of the reaction results.
Eco-Friendly and Cost-Effective
In today’s environmentally conscious world, the eco-friendly nature of glass reactors is a significant advantage. Glass is a sustainable material that can be recycled, reducing the environmental footprint of the equipment. Additionally, the durability and longevity of glass reactors make them a cost-effective investment in the long run, as they require less frequent replacement compared to reactors made from other materials.
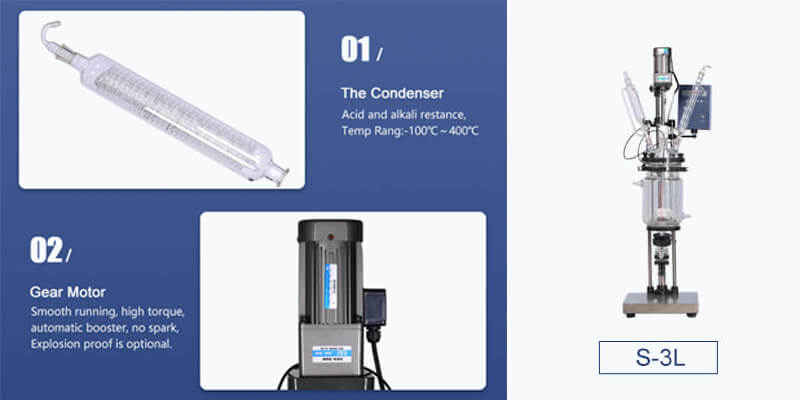
Applications Across Industries
The applications of jacketed glass reactors span across various industries:
Pharmaceuticals: Used for drug synthesis, crystallization, and extraction processes.
Chemicals: Ideal for developing new chemical compounds and processes.
Biotechnology: Employed in the fermentation and culture of microorganisms.
Food and Beverage: Used in the development of flavors, fragrances, and food additives.
Academia and Research: Essential for conducting a wide range of chemical experiments.
Case: Pharmaceutical Industry
Consider a pharmaceutical company developing a new drug. The synthesis of this drug requires precise temperature control to ensure the correct formation of the active ingredient. By using a jacketed glass reactor, the company can maintain the required temperature throughout the process, resulting in a high-purity product with minimal impurities. The visual monitoring feature allows researchers to observe the reaction and make necessary adjustments in real-time, ensuring the process stays on track.
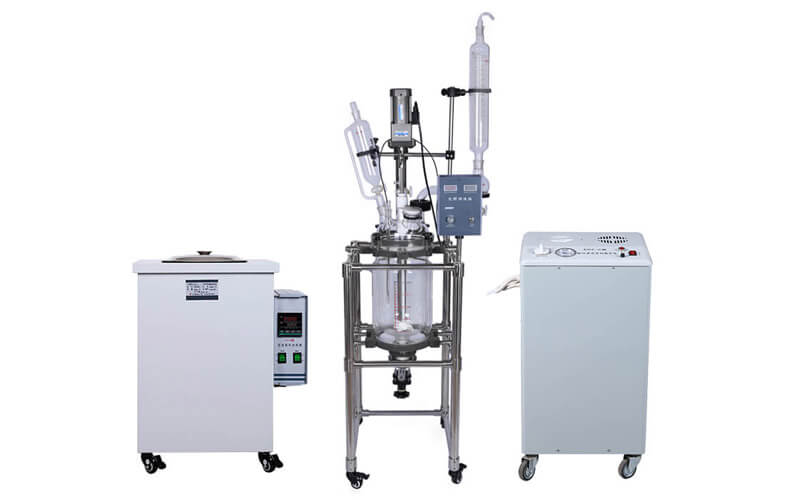
Investing in the Right Equipment
When it comes to choosing the right equipment for your operations, several factors need to be considered. The size of the reactor, the type of glass, the jacket configuration, and additional features should all align with your specific needs. Are you looking for a reactor that offers precise temperature control, efficient mixing, and easy maintenance? A jacketed glass reactor might be the perfect solution for you.
Jacketed glass reactor is a versatile, reliable, and efficient piece of equipment that offers numerous advantages across various industries. Its ability to provide precise temperature control, ensure safety, and offer customization options makes it an invaluable asset in both research and industrial settings. By investing in a jacketed glass reactor, you can enhance your process efficiency, ensure high-quality results, and achieve greater flexibility in your operations. So, why wait? Explore the benefits of jacketed glass reactors and see how they can transform your chemical processes.