In the realm of industrial processing, the quest for efficient and economical methods of transforming liquids into powders is perpetual. Spray drying, a technique that rapidly dries a liquid or slurry by transforming it into a spray of fine droplets which are then dried by hot air, stands as a cornerstone in this domain. However, the question that often surfaces is: Is spray drying cost-effective?
Understanding Spray Drying
Spray drying is not a new technology; it has been around for over a century. Its primary appeal lies in its ability to produce powders with specific properties, including particle size, moisture content, and flowability, which are critical in various industries like pharmaceuticals, food, and chemicals. The process is straightforward: a liquid feed is atomized into a hot drying medium, causing the solvent to evaporate rapidly, leaving behind fine particles.
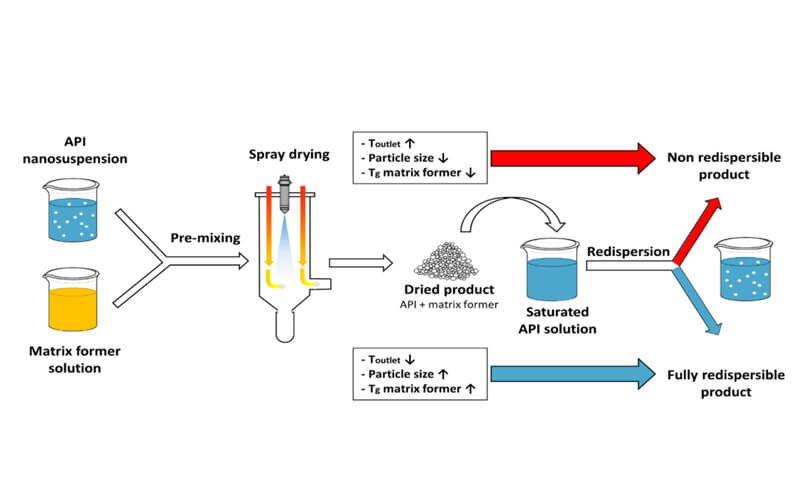
But how does one measure cost-effectiveness in this context? It's essential to consider multiple factors, including operational costs, yield efficiency, product quality, and scalability.
Operational Costs
At first glance, the operational costs of spray drying might seem high due to the energy required to generate the hot air and the equipment's capital investment. However, a deeper analysis reveals that spray drying can be quite economical when viewed through the lens of long-term operation and large-scale production.
Energy Efficiency
Modern spray dryers are designed with energy efficiency in mind. For instance, many systems recapture and reuse the heat generated, significantly reducing energy consumption. Moreover, the efficiency of the process means that it can handle large volumes of material quickly, reducing labor costs and time.
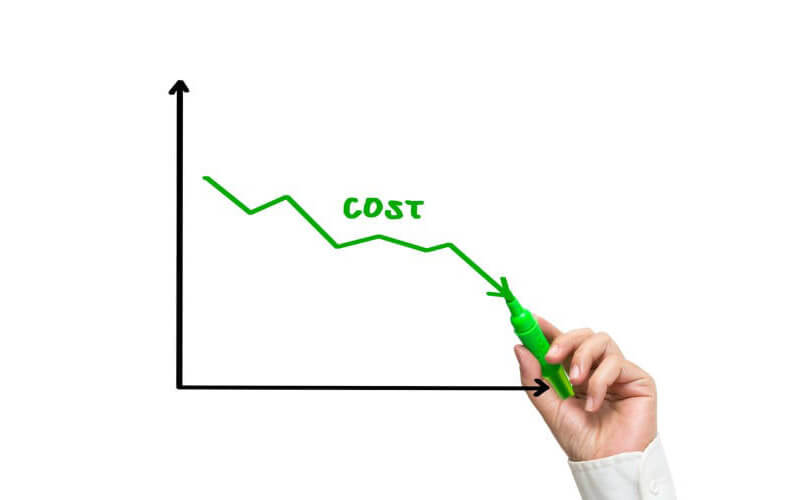
Equipment Investment
While the initial investment in a spray dryer might be considerable, it's crucial to factor in the longevity and durability of these machines. High-quality spray dryers, such as pilot spray dryers, are built to last and can operate continuously with minimal maintenance. This durability spreads the cost over many years of operation, lowering the effective annual cost.
Raw Material Utilization
Spray drying is highly efficient in terms of raw material usage. The process can be finely tuned to minimize waste, ensuring that nearly all the input material is converted into the desired product. This high yield can significantly lower the cost per unit of production.
Yield Efficiency
Yield efficiency is a pivotal factor in determining cost-effectiveness. Spray drying often achieves yields of over 95%, which means minimal raw material is wasted. This high yield directly translates to cost savings, especially when dealing with expensive inputs.
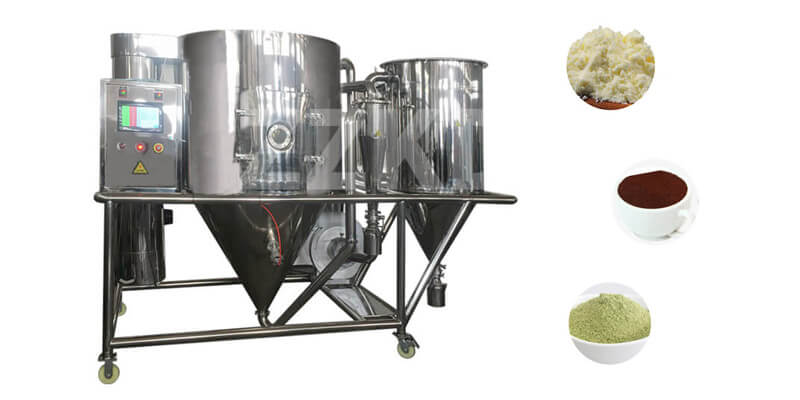
Product Quality and Consistency
One of the hallmarks of spray drying is the consistent quality of the final product. The process produces uniform particles with precise control over moisture content and particle size. This consistency is crucial for industries like pharmaceuticals and food, where product quality directly impacts safety and efficacy.
Reduction in Waste
By optimizing the spray drying process, companies can significantly reduce waste. For instance, the use of pilot spray dryers allows for small-scale testing and optimization before full-scale production. This step ensures that the process parameters are well-defined and efficient, further enhancing cost-effectiveness.
Scalability
Is spray drying scalable for large operations?
Absolutely. One of the significant advantages of spray drying is its scalability. Whether producing small batches in a pilot spray dryer or large volumes in an industrial-scale unit, the process remains efficient and economical.
Pilot Spray Dryers
Pilot spray dryers play a crucial role in scaling up operations. They allow for the testing and optimization of processes on a smaller scale before full-scale implementation. This step not only ensures that the process is efficient but also helps in fine-tuning parameters to maximize yield and minimize costs.
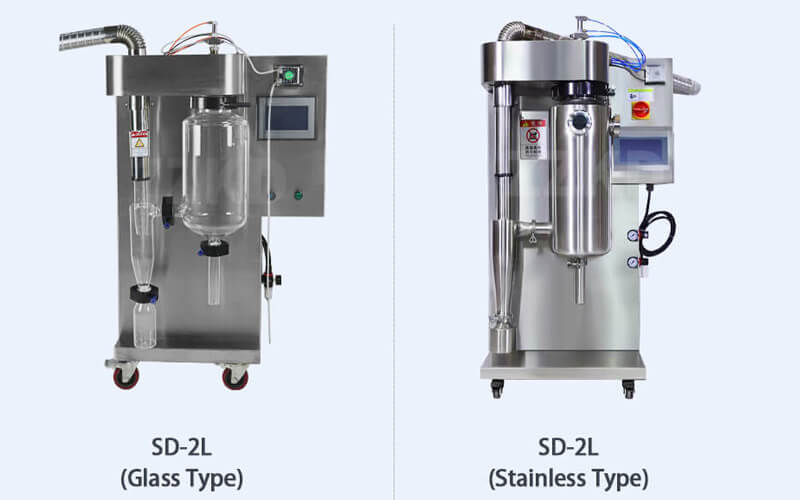
Pilot Spray Dryers
Versatility
Another aspect that adds to the cost-effectiveness of spray drying is its versatility. Spray dryers can handle a wide range of materials, from heat-sensitive pharmaceuticals to robust chemicals and food products. This versatility means that a single spray drying system can be used for multiple products, spreading the capital investment over several revenue streams.
Adaptability to Different Products
The adaptability of spray dryers to different products without significant modifications enhances their utility. This feature is particularly beneficial for companies looking to diversify their product offerings without incurring substantial additional costs.
Environmental Impact
With increasing awareness and regulatory pressure regarding environmental sustainability, the environmental impact of manufacturing processes is a critical consideration. Spray drying can be more environmentally friendly compared to other drying methods.
Energy Consumption
Although spray drying does require energy, modern systems are designed to be energy efficient. Techniques such as heat recovery and the use of renewable energy sources can further reduce the environmental footprint. Moreover, the ability to precisely control the process minimizes the overuse of resources.
Waste Reduction
The high yield efficiency and minimal waste production also contribute to a lower environmental impact. This factor not only makes spray drying cost-effective but also aligns with sustainable manufacturing practices.
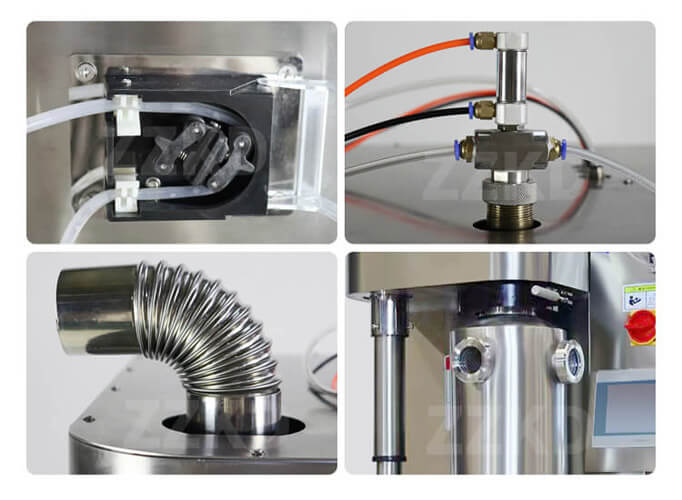
Practical Considerations
When evaluating the cost-effectiveness of spray drying, practical considerations play a vital role. For instance, how does one ensure the process remains efficient and economical over time?
Maintenance and Downtime
Regular maintenance is crucial for ensuring the longevity and efficiency of spray drying equipment. However, modern spray dryers are designed for easy maintenance, with features that allow for quick cleaning and parts replacement, minimizing downtime and associated costs.
Operator Training
Effective operator training can significantly impact the cost-effectiveness of spray drying. Well-trained operators can optimize the process, troubleshoot issues promptly, and maintain the equipment correctly, ensuring the system runs efficiently and reducing operational costs.
Real-World Applications
Several industries have successfully implemented spray drying to enhance their production processes and reduce costs. For instance, the pharmaceutical industry uses spray drying to produce consistent, high-quality powders essential for drug formulation. In the food industry, spray drying is used to create powdered milk, coffee, and flavors, ensuring long shelf life and easy transportation.
Numerous case studies demonstrate the cost-effectiveness of spray drying. For example, a food processing company transitioning from traditional drying methods to spray drying saw a significant reduction in production costs and an improvement in product quality. Similarly, a pharmaceutical firm using a pilot spray dryer for R&D purposes was able to scale up to full production efficiently, saving time and resources.
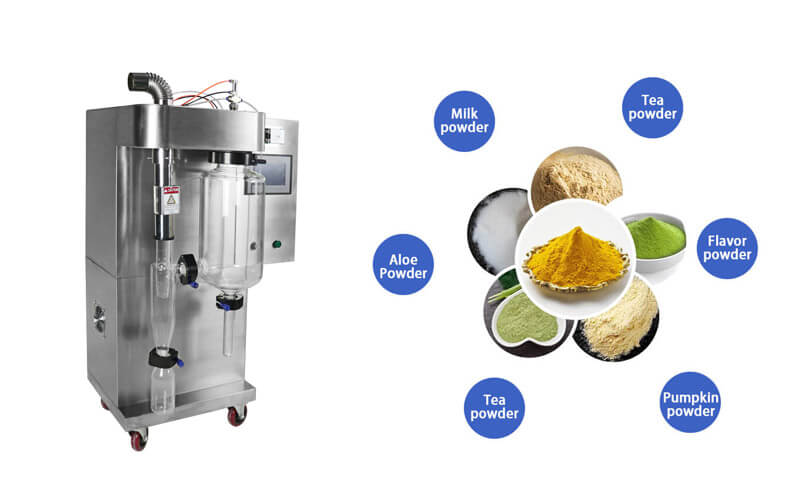
So, is spray drying cost-effective? When considering operational costs, yield efficiency, product quality, scalability, and environmental impact, the answer is a resounding yes. The initial investment in equipment is offset by the long-term savings in energy, raw materials, and labor. Moreover, the consistent quality and versatility of spray-dried products open up new opportunities for innovation and market expansion.
Are there challenges? Certainly, but with proper planning, investment in high-quality equipment like pilot spray dryers, and ongoing optimization, these challenges can be managed effectively. Thus, for industries looking to improve their production processes and reduce costs, spray drying presents a viable and cost-effective solution.
Would transitioning to spray drying improve operational efficiency? The evidence strongly suggests so. By embracing this technology, companies can enhance their competitiveness and achieve long-term success in a demanding market.