High pressure autoclave reactors are critical components in the realm of chemical engineering, enabling sophisticated reactions and processes under elevated pressure and temperature conditions.
High pressure autoclave reactors are specialized vessels designed to accommodate chemical reactions and processes that require elevated pressure and temperature conditions. These reactors are engineered to withstand high internal pressures, ensuring the safety and integrity of the reaction environment.
The design and construction of high pressure autoclave reactors involve the use of robust materials such as stainless steel or high-performance alloys to withstand the extreme conditions experienced during operation. This enables researchers and engineers to explore a wide range of chemical transformations and processes with precision and control.
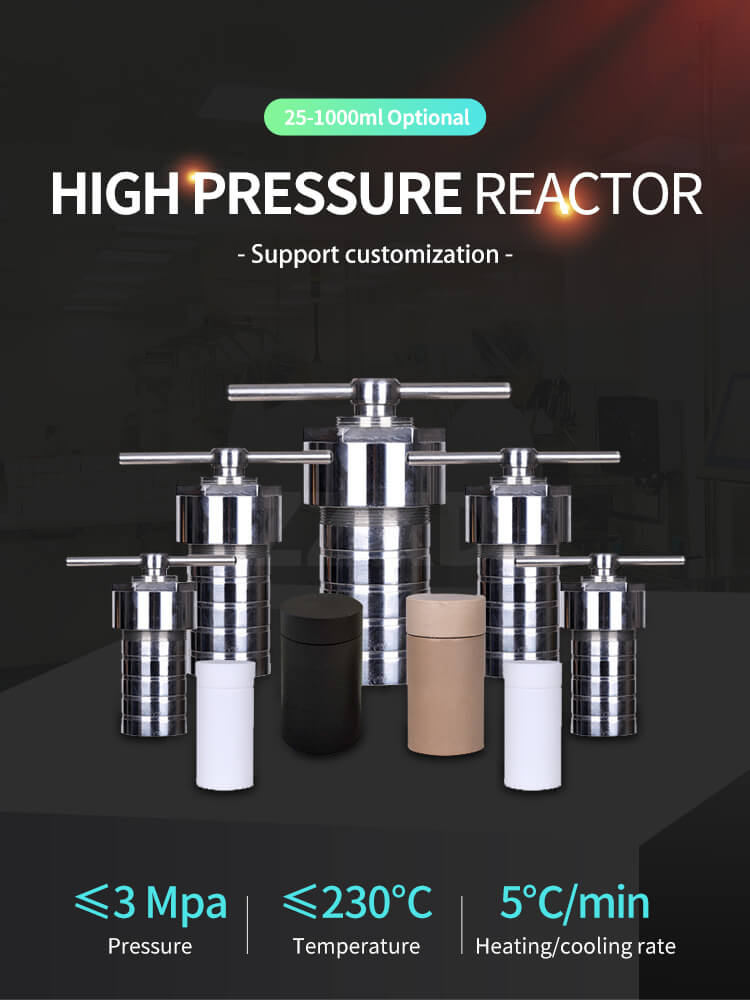
Operating Principles of High Pressure Autoclave Reactors
High pressure autoclave reactors operate on the principle of confining reactions within a controlled environment, where pressure and temperature can be precisely regulated to drive chemical transformations. The reactor vessel, equipped with pressure-resistant seals and fittings, ensures containment of the reaction medium under high pressure conditions.
The reactor's operating parameters, including pressure, temperature, stirring speed, and reaction time, are carefully controlled and monitored to optimize reaction kinetics, product yields, and selectivity. This level of control is essential for achieving desired outcomes in complex chemical processes, including catalysis, polymerization, and hydrogenation reactions.
Key Components of High Pressure Autoclave Reactors
High pressure autoclave reactors consist of several key components:
1. Reactor Vessel: The primary component of the autoclave reactor, the vessel is designed to contain the reaction medium under high pressure conditions. It is typically constructed from corrosion-resistant materials capable of withstanding elevated temperatures and pressures.
2. Heating and Cooling Systems: Autoclave reactors are equipped with heating and cooling systems to control the temperature of the reaction medium. These systems ensure precise temperature control, enabling researchers to optimize reaction conditions and achieve desired outcomes.
3. Pressure Control Mechanisms: Pressure control mechanisms, such as pressure relief valves and safety interlocks, are integrated into autoclave reactors to ensure the safety of personnel and equipment. These mechanisms prevent over-pressurization of the reactor vessel and mitigate the risk of accidents.
4. Stirring Mechanism: Autoclave reactors are equipped with stirring mechanisms to facilitate mixing and homogenization of the reaction medium. The stirring speed can be adjusted to optimize mass transfer and reaction kinetics, ensuring uniform distribution of reactants and products.
5. Instrumentation and Control Systems: Autoclave reactors are equipped with instrumentation and control systems to monitor and regulate key process parameters in real-time. These systems provide operators with valuable insights into the progress of the reaction and enable adjustments to optimize performance.
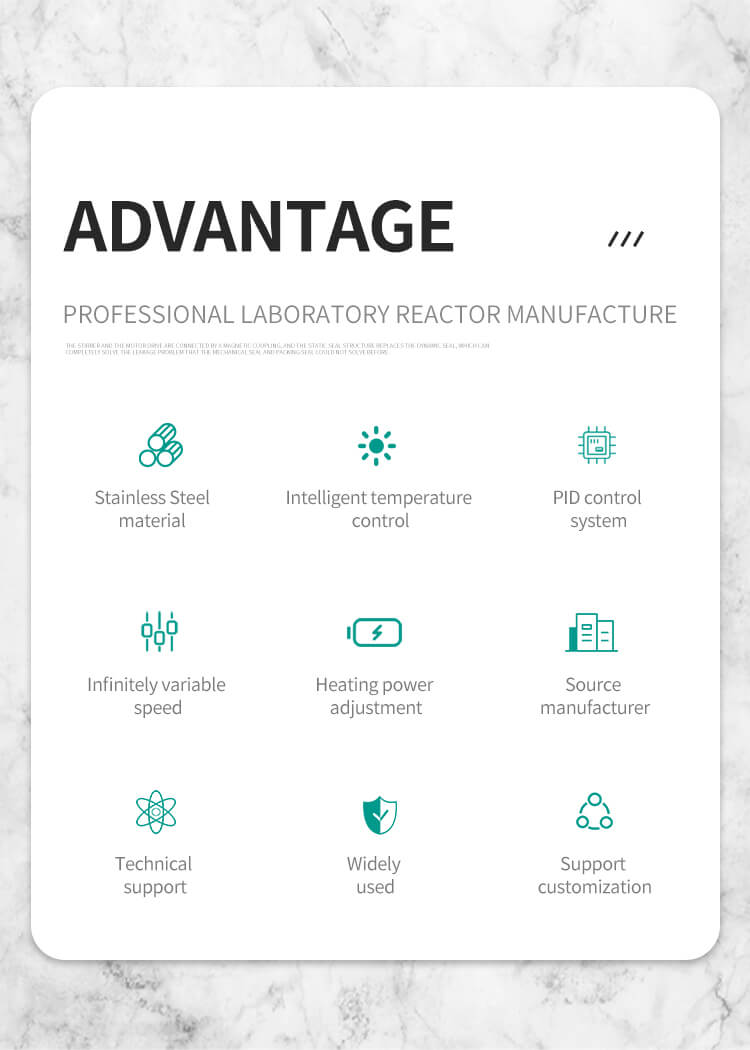
Applications of the High Pressure Autoclave Reactor
High pressure autoclave reactors find applications across a diverse range of industries and research disciplines:
Industry
|
Materials Used
|
High Pressure Reactor Model
|
Parameters
|
Pharmaceutical
|
Active pharmaceutical ingredients, solvents
|
CJF-10
|
Capacity (L): 10, Setting Pressure (MPa): 22, Setting Temperature (℃): 350, Heating Power (kW): 7, Stirring Torque (N. cm): 120, Voltage (V/Hz): 220V/50/60Hz
|
Chemical
|
Specialty chemicals, polymerization
|
CF-5
|
Capacity (L): 5, Setting Pressure (MPa): 10, Setting Temperature (℃): 350, Heating Power (kW): -, Stirring Torque (N. cm): -, Voltage (V/Hz): -
|
Food Processing
|
Flavor extracts, food additives
|
CF-0.5
|
Capacity (L): 0.5, Setting Pressure (MPa): 22, Setting Temperature (℃): 304L/316L, Heating Power (kW): -, Stirring Torque (N. cm): -, Voltage (V/Hz): -
|
Petrochemical
|
Petrochemical intermediates, polymers
|
FCF-5
|
Capacity (L): 5, Setting Pressure (MPa): 22, Setting Temperature (℃): 350, Heating Power (kW): 4, Stirring Torque (N. cm): 120, Voltage (V/Hz): 220V/50/60Hz
|
Environmental
|
Soil remediation agents, wastewater treatment
|
CJF-20
|
Capacity (L): 20, Setting Pressure (MPa): 22, Setting Temperature (℃): 350, Heating Power (kW): 10, Stirring Torque (N. cm): 120, Voltage (V/Hz): 220V/50/60Hz
|
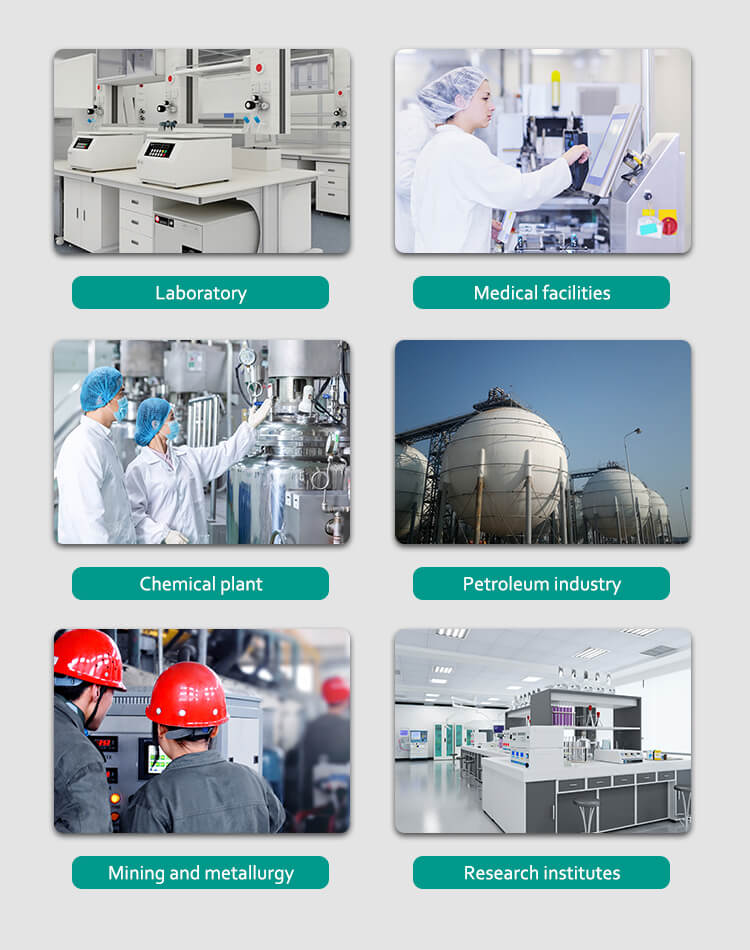
Note:
1. Ensure operators are trained in the specific operation and safety procedures for each High Pressure Reactor model.
2. Strictly adhere to safety guidelines and protocols provided in the manual for each machine.
3. Regular maintenance and inspection of the High Pressure Reactor are essential for optimal performance.
4. Utilize appropriate personal protective equipment (PPE) such as goggles, gloves, and lab coats when handling materials.
5. Work with volatile or hazardous materials in well-ventilated areas or under appropriate containment measures.
6. Follow proper waste disposal procedures in accordance with regulations.
7. Monitor process parameters like pressure, temperature, and stirring torque to prevent accidents and ensure efficiency.
Considerations for Selecting High Pressure Autoclave Reactors
When selecting a high pressure autoclave reactor, several factors should be considered:
1. Pressure and Temperature Range: Choose a reactor that offers the required pressure and temperature range to accommodate your specific application and process requirements.
2. Material Compatibility: Ensure that the reactor materials are compatible with the reaction medium and any corrosive or reactive substances involved in the process.
3. Safety Features: Look for reactors equipped with robust safety features, including pressure relief valves, safety interlocks, and emergency shutdown systems, to mitigate the risk of accidents and ensure operator safety.
4. Ease of Use and Maintenance: Select a reactor that is user-friendly and easy to maintain, with intuitive controls and accessible components for routine maintenance and servicing.
5. Scalability: Consider the scalability of the reactor system to accommodate future expansion or changes in process requirements. Choose a reactor platform that offers flexibility and adaptability to evolving research and production needs.
High pressure autoclave reactors are available in a diverse range of sizes and configurations tailored to meet a wide spectrum of application requirements. Compact tabletop models like the FCF-0.1 and FCF-1 are specifically designed for laboratories with limited space. These autoclaves feature capacities ranging from 0.1 liters to 1 liter, operating pressures up to 22 MPa, and temperatures up to 350°C. Additionally, they are equipped with heating systems of up to 1.5 kW and stirring torques of 120 N. cm.
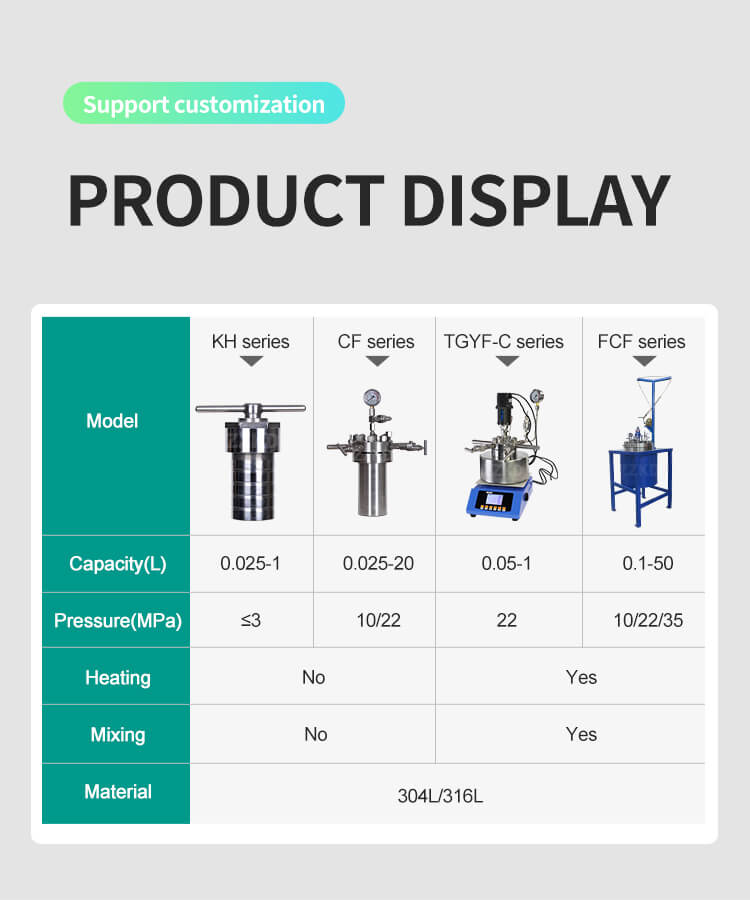
Model
|
Capacity(L)
|
Pressure(MPa)
|
Material
|
CF-0.05
|
0.05
|
22
|
304L/316L
|
CF-0.1
|
0.1
|
22
|
304L/316L
|
CF-0.2
|
0.2
|
22
|
304L/316L
|
CF-0.5
|
0.5
|
22
|
304L/316L
|
CF-1
|
1
|
22
|
304L/316L
|
CF-5
|
5
|
10
|
304L/316L
|
CF-10
|
10
|
22
|
304L/316L
|
CF-20
|
20
|
22
|
304L/316L
|
High Pressure Autoclave Reactor
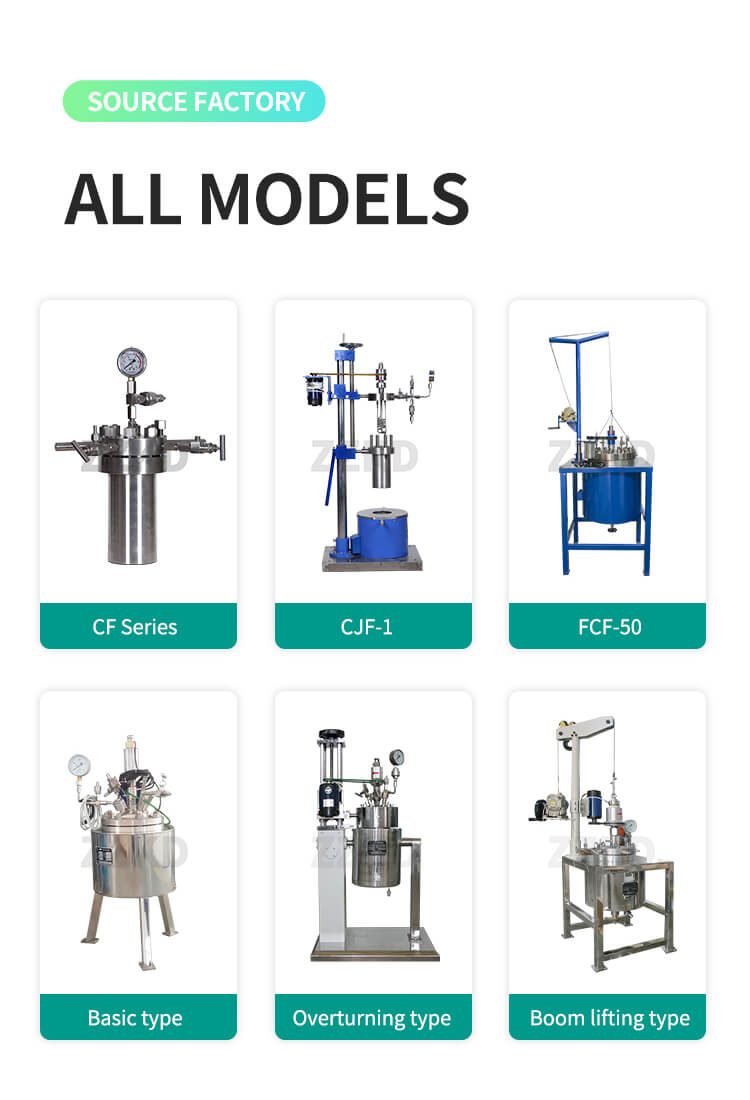
Model
|
Capacity (L)
|
Setting Pressure (MPa)
|
Setting Temperature (℃)
|
Stirring Torque (N. cm)
|
FCF-0.1
|
0.1
|
22
|
350
|
120
|
FCF-1
|
1
|
22
|
350
|
120
|
FCF-5
|
5
|
22
|
350
|
120
|
FCF-20
|
20
|
22
|
350
|
120
|
FCF-50
|
50
|
10
|
350
|
120
|
FCF-100
|
100
|
60
|
350
|
120
|
CJF-5
|
5
|
22
|
350
|
120
|
CJF-10
|
10
|
22
|
350
|
120
|
CJF-20
|
20
|
22
|
350
|
120
|
CJF-30
|
30
|
22
|
350
|
120
|
High Pressure Reactor
On the other hand, larger-scale autoclaves such as the FCF-20, FCF-50, and FCF-100 are designed for expanded applications. These models offer capacities ranging from 20 liters to 100 liters, operating pressures up to 60 MPa, and temperatures up to 350°C. They feature heating systems of up to 14 kW and stirring torques of 120 N. cm.
These high pressure autoclave reactors can be seamlessly integrated with a variety of accessories and automation features to optimize workflow efficiency and meet the diverse needs of modern scientific endeavors.
Why Choose Our High Pressure Autoclave Reactors
Our high pressure autoclave reactors are engineered to meet the most demanding process requirements, offering unmatched performance, reliability, and safety. With a commitment to quality and innovation, we deliver state-of-the-art reactor systems designed to empower researchers and engineers in their quest for scientific discovery and process optimization.
Our reactors feature advanced design principles, precision engineering, and robust construction materials to ensure optimal performance and longevity in the most challenging environments. We offer a comprehensive range of reactor configurations and customization options to suit a variety of applications and process requirements.
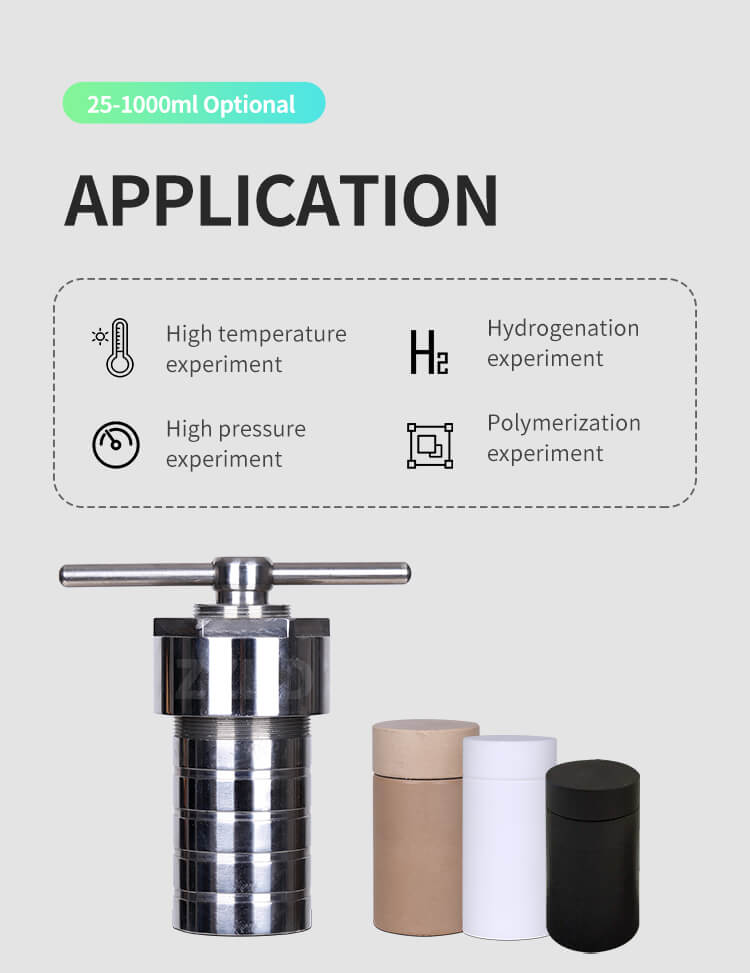
In addition to our industry-leading products, we provide exceptional customer support and technical expertise to guide you through every step of the reactor selection, installation, and operation process. Our team of experienced engineers and scientists is dedicated to helping you achieve your research and production goals with confidence and efficiency.
With our high pressure autoclave reactors, you can unlock new possibilities, explore innovative processes, and accelerate your journey towards scientific excellence and technological advancement. Choose quality, choose reliability, choose innovation—choose our high pressure autoclave reactors for your next chemical engineering endeavor.