Understanding the Role of Pressure Vessels in Chemical Processes
Pressure vessels play a crucial role in chemical processes by ensuring the safe containment of reactive substances under high pressure. These vessels are designed to withstand the extreme conditions that arise during chemical reactions, protecting both the operators and the surrounding environment. Compliance with safety regulations is essential for their effective use, as it helps prevent accidents and ensures the reliability of these vessels. By providing a controlled environment for 100 liter glass reactor, pressure vessels enable efficient and precise processing of various substances. Understanding their importance is vital for chemical engineers, students, and professionals in the industry to ensure the safe and successful operation of chemical processes.

Safety Considerations and Regulations
Pressure vessels must be designed and operated with safety as the top priority. Considering the potential risks associated with high-pressure systems, it is crucial to implement proper safety considerations. This includes designing pressure vessels to withstand the intended operating conditions, ensuring structural integrity, and preventing leaks or failures.
Proper maintenance and regular inspections are essential for preventing accidents. Regular checks help identify any signs of wear, corrosion, or damage that could compromise the vessel's integrity. By addressing these issues promptly, potential hazards can be mitigated before they escalate into more significant problems.
Safety relief devices and pressure gauges are crucial components of pressure vessels. Relief devices such as pressure relief valves protect against overpressure situations by releasing excess pressure from the vessel. Pressure gauges provide real-time monitoring of internal pressures, allowing operators to maintain safe operating conditions within the vessel.
Pressure vessel design and operation are regulated by industry standards to ensure safe practices across the chemical industry. Compliance with codes and regulations is necessary to guarantee safe and reliable operation. These standards outline specific requirements for design, fabrication, inspection, testing, and maintenance of pressure vessels.
Inspections and certifications play a vital role in meeting regulatory requirements. Periodic inspections help verify that pressure vessels are in good condition and functioning correctly. Certifications provide assurance that a vessel meets all necessary safety standards and has undergone thorough testing.
By prioritizing safety considerations and adhering to relevant regulations, chemical engineers can ensure the effective use of pressure vessels in chemical processes while minimizing risks to personnel, equipment, and the environment.
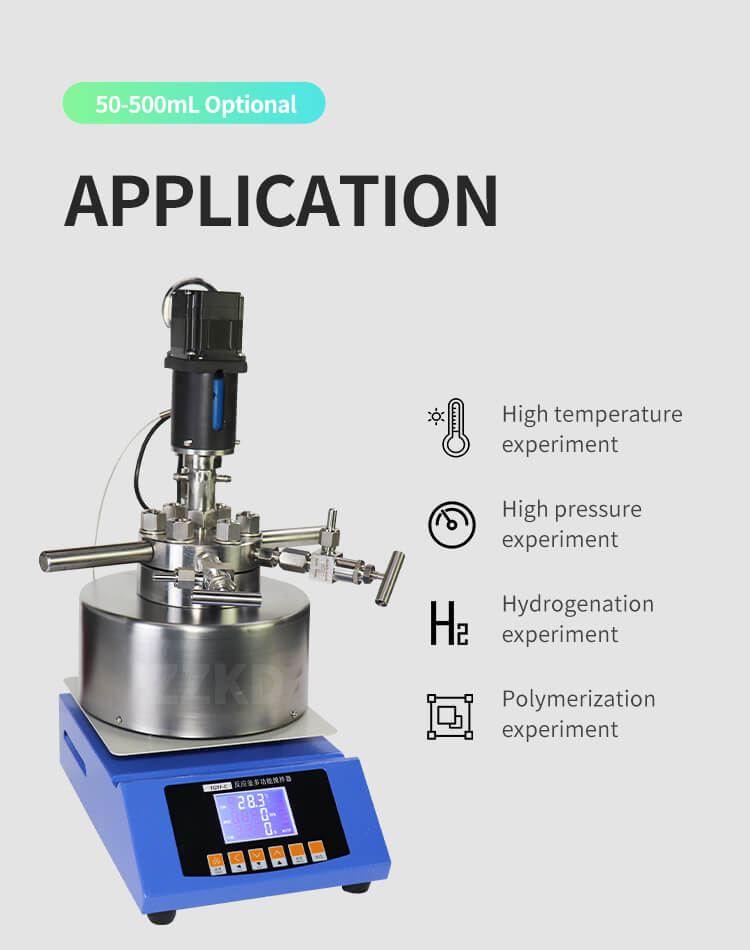
Types and Features of Glass Reactor Pressure Vessels
Glass reactor pressure vessels are widely used in chemical processes due to their unique properties and advantages. Understanding the different types and key features of these vessels is essential for selecting the most suitable option for specific applications.
Different Types of Glass Reactor Pressure Vessels
Single-walled glass reactors: These vessels are suitable for low-pressure applications where temperature control is not a critical factor. They provide a cost-effective solution for basic chemical reactions.
Double-walled glass reactors: Designed with an additional layer, these vessels offer enhanced safety and insulation. The double-wall construction helps prevent heat loss or gain, making them ideal for reactions requiring precise temperature control.
Triple-walled glass reactors: These advanced vessels provide even higher safety levels and superior temperature control capabilities. The triple-wall design offers excellent insulation, minimizing heat transfer to the surroundings and ensuring optimal reaction conditions.
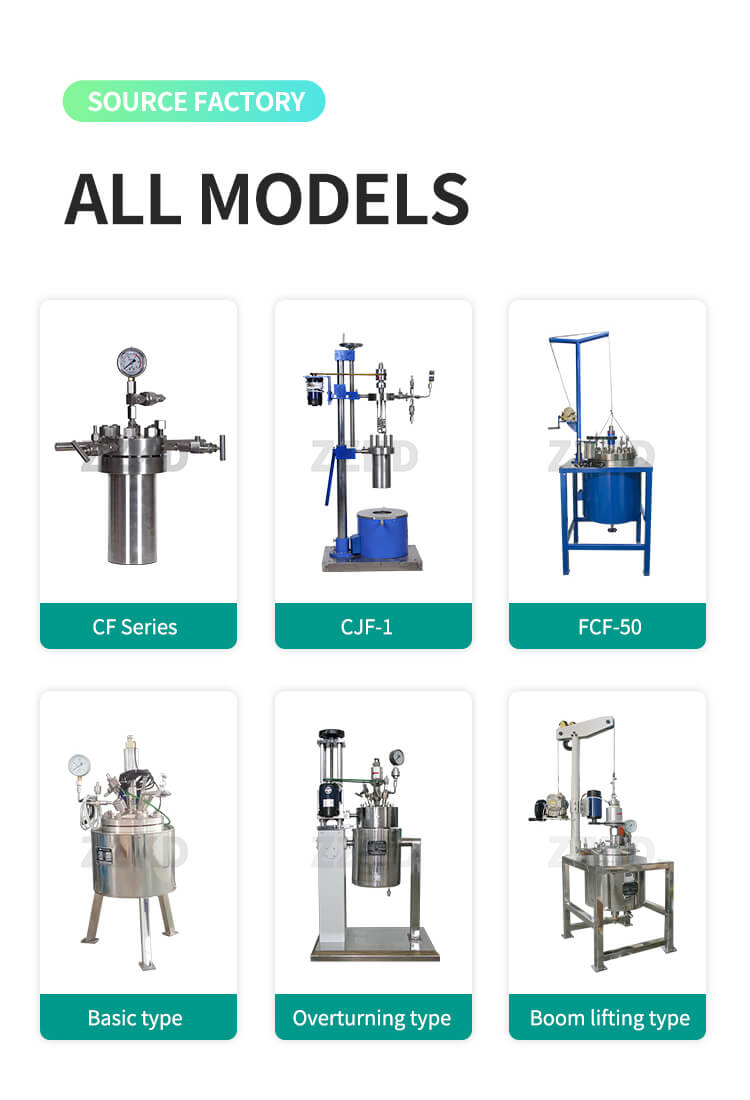
Key Features of Glass Reactor Pressure Vessels
High-quality borosilicate glass: Glass reactor pressure vessels are typically made from borosilicate glass, known for its exceptional chemical resistance and durability. This ensures compatibility with a wide range of substances and extends the lifespan of the vessel.
Precise temperature control: Temperature plays a crucial role in many chemical reactions. Glass reactor pressure vessels allow for precise temperature control, enabling researchers to maintain optimal reaction conditions throughout the process.
Modular designs and customizable options: These vessels often feature modular designs that can be easily adapted to specific process requirements. Customizable options include different sizes, configurations, accessories, and additional features tailored to meet individual needs.
By understanding the various types available and considering key features such as material quality, temperature control capabilities, and customization options, chemical engineers can select the most appropriate glass reactor pressure vessel for their specific applications.
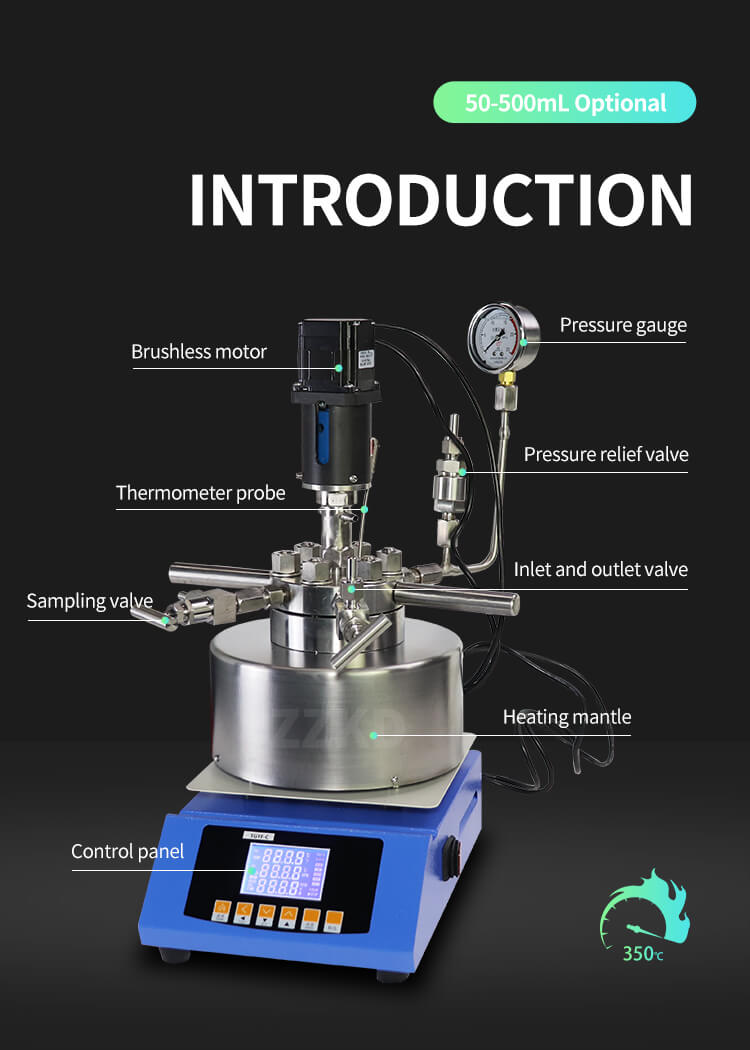
The Crucial Role of Pressure Vessels in Chemical Processes
Pressure vessels play a crucial role in chemical processes by ensuring the safe containment of reactive substances. They provide a controlled environment for reactions to take place under high pressure, protecting both operators and the surrounding environment from potential hazards. Adhering to safety regulations is essential to ensure their effective and reliable use. By following industry standards and implementing proper safety considerations, pressure vessels can be utilized with confidence. Glass reactor pressure vessels, in particular, offer specific advantages such as chemical resistance, precise temperature control, and customizable options that cater to the unique requirements of chemical processes. Overall, pressure vessels are indispensable tools that enable efficient and safe chemical reactions in various industries.