Borosilicate glass reactors play a pivotal role in various industries, serving as essential equipment for chemical synthesis, pharmaceutical development, and scientific research. These vessels provide a controlled environment for chemical reactions, offering a transparent and versatile solution for observing and manipulating reactions. In this article, we will explore what borosilicate glass reactors are, their working principles, and the advantages they offer.
What is a Borosilicate Glass Reactor?
A borosilicate glass reactor, also known as a glass reaction vessel or glass reactor, is a container typically made of borosilicate glass, designed to contain chemical reactions under controlled conditions. These vessels come in various shapes and sizes, ranging from small-scale laboratory setups to large industrial reactors. The primary purpose of a glass reactor vessel is to facilitate chemical reactions while allowing researchers or operators to monitor the progress visually.
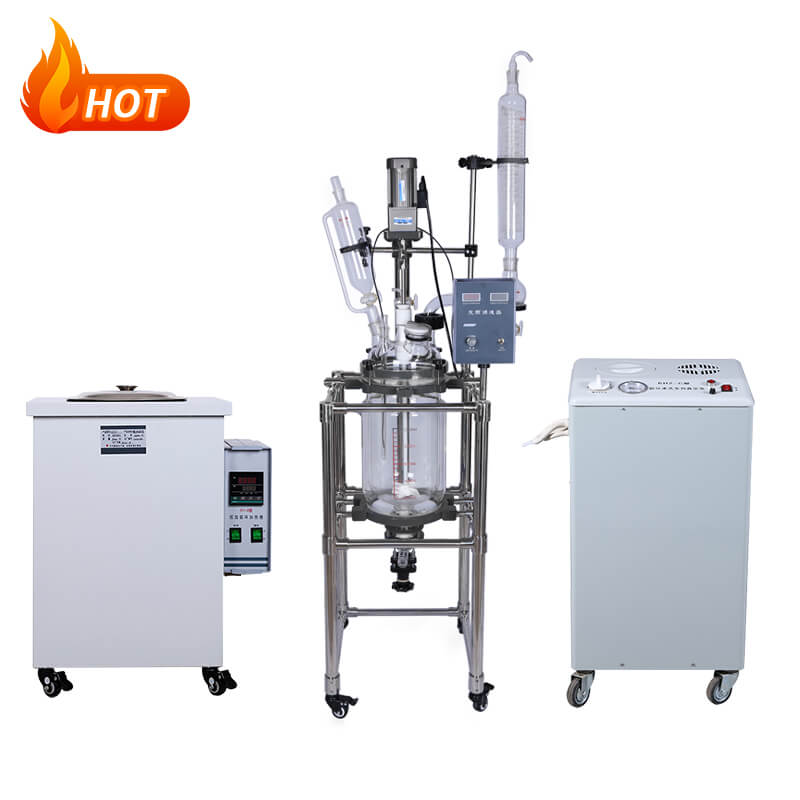
How Does a Borosilicate Glass Reactor Work?
The working principle of a borosilicate glass reactor revolves around creating a controlled environment for chemical reactions to occur. Here's a brief overview of how it operates:
1. Containment: The reaction mixture, along with any necessary reagents or catalysts, is placed inside the borosilicate glass reactor.
2. Controlled Environment: The vessel is sealed to prevent any leakage or contamination from external factors. This ensures that the reaction occurs in a controlled environment, free from interference.
3. Temperature Control: Many borosilicate glass reactors come equipped with heating or cooling systems to maintain the desired temperature for the reaction. This temperature control is crucial for optimizing reaction rates and selectivity.
4. Stirring Mechanism: To ensure uniform mixing of reactants and promote efficient mass transfer, most borosilicate glass reactors incorporate a stirring mechanism. This can range from simple magnetic stirrers to more advanced agitation systems.
5. Observation: One of the key advantages of borosilicate glass reactors is their transparency, allowing researchers to observe the reaction in real-time. This visual feedback is invaluable for monitoring reaction progress, identifying any issues, and making adjustments as necessary.
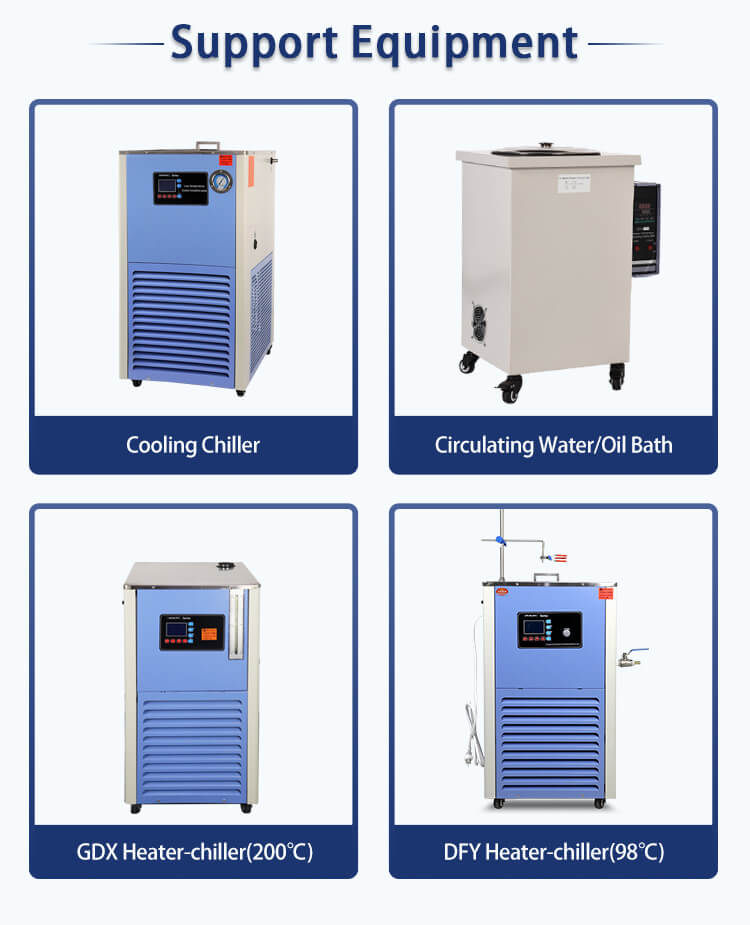
Benefits of Borosilicate Glass Reactor
Borosilicate glass reactors offer several advantages over alternative reaction vessels, making them a popular choice in research laboratories and industrial settings:
1. Visibility: The transparency of glass allows for direct observation of the reaction, enabling researchers to visually inspect color changes, phase separations, and other important indicators of reaction progress.
2. Chemical Inertness: Borosilicate glass, commonly used in reactor vessels, is highly resistant to chemical attack, making it suitable for a wide range of corrosive reactions. This inertness ensures that the vessel itself does not interfere with the reaction or contaminate the products.
3. Versatility: Borosilicate glass reactors can accommodate various types of chemical reactions, including synthesis, crystallization, distillation, and reflux, making them versatile tools for chemists and researchers.
4. Scalability: Borosilicate glass reactors are available in a range of sizes, from small-scale benchtop units to large industrial reactors, allowing for seamless scalability from laboratory development to industrial production.
5. Ease of Cleaning: Glass is easy to clean and sterilize, reducing the risk of cross-contamination between different reactions.
6. Safety: Unlike metal reactors, borosilicate glass reactors do not pose the risk of metal contamination or sparking, making them safer for use in reactive or flammable reactions.
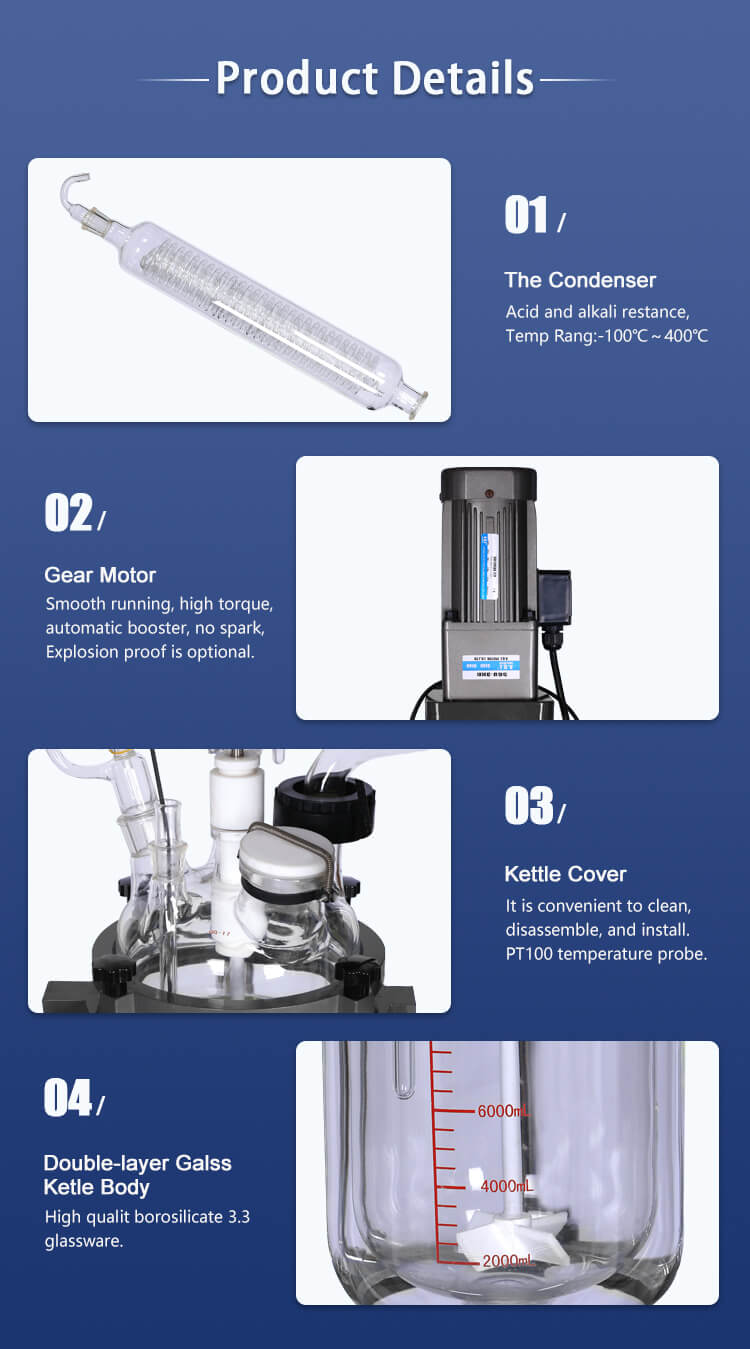
Is Investing in a Borosilicate Glass Reactor a Wise Decision for Businesses?
Absolutely, the decision to invest in a borosilicate glass reactor can prove highly beneficial for businesses. However, the extent of these benefits varies depending on the company's specific needs and objectives. When contemplating such an investment, businesses often have diverse motivations. Some prioritize cost reduction in chemical processes, while others focus on meeting environmental standards or improving production efficiency. Like customers considering different factors when choosing products, such as price, quality, and reliability, businesses must also carefully assess various factors to select the most suitable borosilicate glass reactorl for their operations.
How Can Customers Determine the Right Borosilicate Glass Reactor for Their Needs?
Customers can evaluate their requirements based on factors like the volume of chemicals processed (daily or monthly) and the types of reactions involved. Borosilicate glass reactors come in various sizes and configurations to accommodate different production capacities. By estimating their monthly chemical processing volume and considering factors like reaction time and efficiency, customers can select the appropriate vessel size. For instance, smaller-scale operations may benefit from a 50-liter vessel, while larger production volumes may require a 200-liter vessel. These decisions should align with the company's production goals and operational requirements.
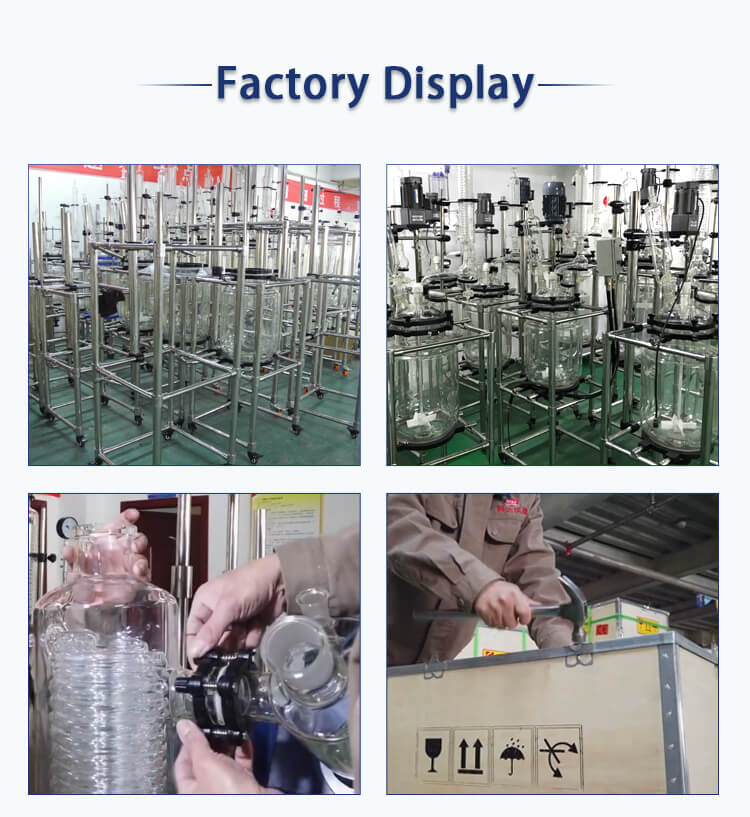
What Are the Key Advantages of Investing in a Borosilicate Glass Reactor?
Investing in a borosilicate glass reactor offers several advantages for businesses. Firstly, it provides precise control over reaction parameters, leading to improved product quality and higher yields. Additionally, borosilicate glass reactors are versatile and compatible with a wide range of chemicals, allowing for flexibility in production processes. Furthermore, these vessels are easy to clean and maintain, contributing to overall operational efficiency. Ultimately, investing in a borosilicate glass reactor enables businesses to streamline their operations, reduce waste, and maintain competitiveness in the market.