In the realm of chemical processing and research, the high pressure chemical reactor stands as a crucial piece of equipment. Known for its versatility and efficiency, this reactor plays an essential role in a wide range of industries, from pharmaceuticals to petrochemicals. Understanding its advantages, applications, and operational capabilities is vital for anyone involved in chemical engineering or related fields.
What Is a High Pressure Chemical Reactor?
A high pressure chemical reactor is a type of vessel designed to carry out chemical reactions under high pressure conditions. These reactors are engineered to withstand pressures that are significantly higher than atmospheric pressure, often ranging from a few bars to several thousand bars. The materials used in their construction, typically stainless steel or other high-strength alloys, ensure that they can handle these extreme conditions without compromising safety or efficiency.
High pressure reactors are used for a variety of purposes, including the synthesis of new chemical compounds, catalysis, and the study of reaction kinetics. They are particularly valuable in processes where high pressure is required to force reactants together or to achieve higher reaction rates.
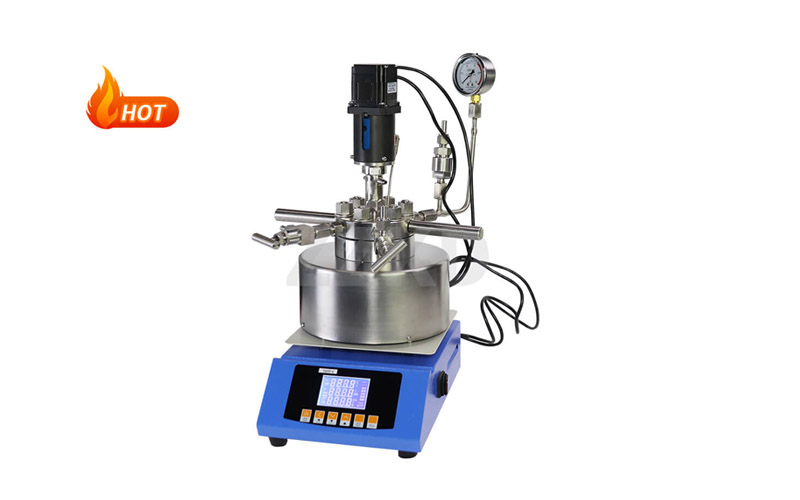
Why Are High Pressure Chemical Reactors Important?
The importance of high pressure chemical reactors lies in their ability to facilitate reactions that would be impossible or impractical under normal atmospheric conditions. By applying high pressure, these reactors can speed up reaction rates, increase yields, and improve the selectivity of certain processes. This makes them indispensable in the development of new materials and chemicals.
For instance, in the pharmaceutical industry, high pressure reactors are often used to synthesize complex organic molecules that are the active ingredients in medications. The ability to control reaction conditions with precision allows chemists to optimize these processes, reducing costs and time-to-market for new drugs.
In the petrochemical industry, high pressure reactors are used to refine crude oil into various products, including gasoline, diesel, and lubricants. The ability to operate at high pressures allows for more efficient cracking and reforming processes, which are essential for converting heavy hydrocarbons into more valuable lighter fractions.
But how does one choose the right high pressure reactor for a specific application? This question is critical because the wrong choice could lead to inefficiencies or even safety hazards.
Key Factors to Consider When Choosing a High Pressure Reactor
Selecting the right high pressure chemical reactor depends on several factors:
-
Pressure and Temperature Requirements: The reactor must be able to withstand the maximum pressure and temperature of the process. For instance, some reactions may require pressures above 500 bars, necessitating a reactor that can safely operate under such conditions.
-
Material Compatibility: The reactor’s construction material must be compatible with the reactants and products to prevent corrosion or contamination. Stainless steel is common, but for more corrosive chemicals, materials like Hastelloy or titanium may be necessary.
-
Volume: The size of the reactor should be appropriate for the scale of the reaction. Lab-scale reactors may only need a few milliliters of volume, while industrial reactors could require several liters or more.
-
Stirring Mechanism: Efficient mixing of reactants is often crucial for achieving uniform reaction conditions. High pressure reactors typically include stirring mechanisms that must be capable of operating under high pressure.
-
Safety Features: High pressure reactions carry inherent risks, so the reactor should be equipped with safety features such as pressure relief valves, burst disks, and fail-safe controls to prevent accidents.
By carefully considering these factors, one can ensure that the chosen reactor will perform optimally for its intended application.
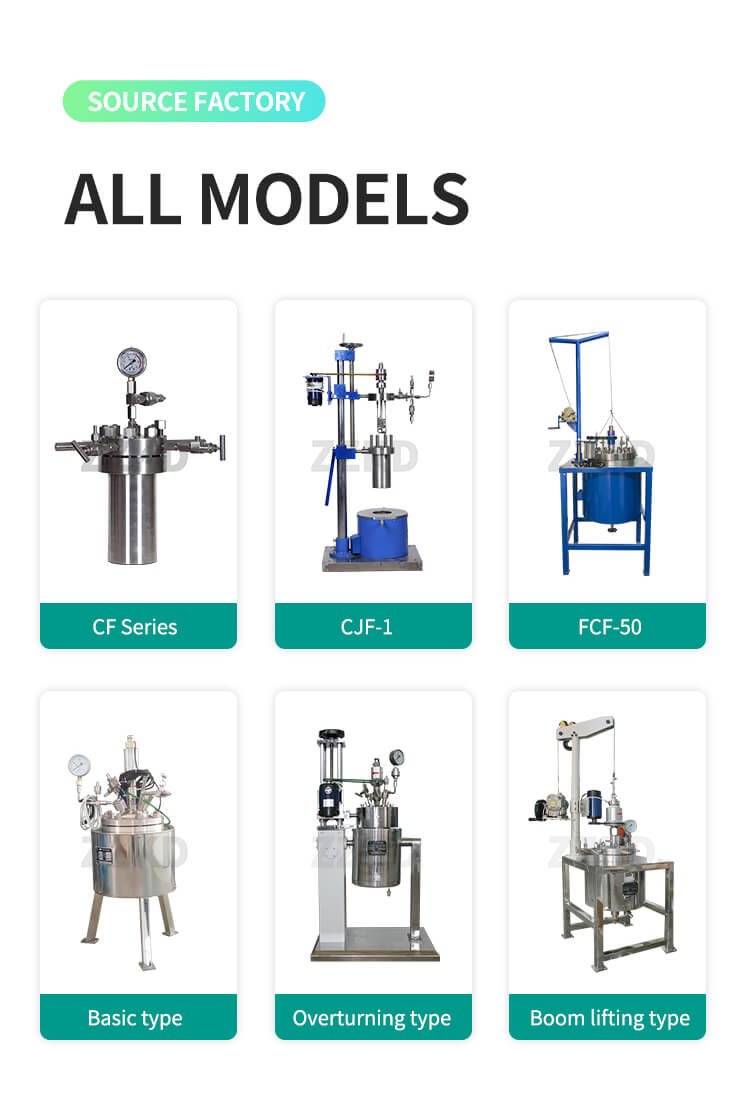
Applications of High Pressure Chemical Reactors
The applications of high pressure chemical reactors are vast and varied, spanning multiple industries. Some of the most common applications include:
-
Catalytic Hydrogenation: This is a critical process in the production of margarine, where unsaturated fats are hydrogenated to produce saturated fats. High pressure reactors are used to dissolve hydrogen gas into the oil, speeding up the reaction and ensuring complete hydrogenation.
-
Ammonia Synthesis: In the production of fertilizers, the Haber-Bosch process uses high pressure reactors to combine nitrogen and hydrogen gases into ammonia. This process operates at pressures up to 200 bars and is vital for the global agricultural industry.
-
Polymerization Reactions: Many polymers, including polyethylene and polypropylene, are produced in high pressure reactors. These reactors provide the necessary conditions for the polymerization reactions to occur efficiently, resulting in high-quality products used in everything from packaging to automotive components.
-
Supercritical Fluid Extraction: This technique is used to extract valuable compounds from natural sources, such as caffeine from coffee beans or essential oils from plants. High pressure reactors allow these extractions to occur at supercritical conditions, where the solvent exhibits unique properties that enhance extraction efficiency.
-
Research and Development: In academic and industrial research, high pressure reactors are used to study the kinetics and mechanisms of chemical reactions. By varying pressure and temperature, researchers can gain insights into how reactions proceed and develop new synthetic pathways for creating novel compounds.
Given these diverse applications, it’s clear that high pressure chemical reactors are a cornerstone of modern chemical engineering. But what are the challenges associated with their use?
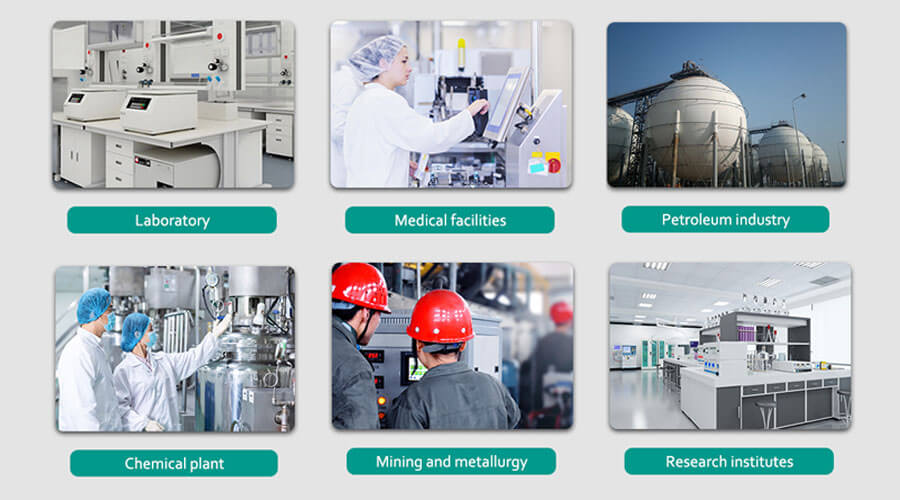
Challenges in Operating High Pressure Chemical Reactors
Operating high pressure chemical reactors presents several challenges, particularly in terms of safety, maintenance, and control. These challenges must be addressed to ensure that the reactors function reliably and safely.
Safety Concerns: High pressure operations inherently carry a higher risk of accidents. The possibility of leaks, explosions, or mechanical failures requires stringent safety protocols. Reactors must be regularly inspected and maintained to ensure that all seals, valves, and pressure-relief systems are functioning correctly.
One might wonder, what steps can be taken to minimize these risks? Regular training for operators, coupled with automated safety systems that can shut down the reactor in the event of an anomaly, are critical measures. Additionally, thorough risk assessments should be conducted before starting any high pressure operation.
Maintenance Requirements: High pressure reactors are subject to significant wear and tear due to the extreme conditions under which they operate. Regular maintenance is essential to prevent failures that could lead to downtime or accidents. This includes checking for corrosion, wear on mechanical components, and ensuring that all safety systems are operational.
Control and Monitoring: Precise control of pressure, temperature, and reaction conditions is crucial for achieving desired outcomes. Modern high pressure reactors are equipped with advanced control systems that allow for real-time monitoring and adjustment of reaction parameters. However, these systems can be complex and require skilled operators to manage them effectively.
Innovations in High Pressure Chemical Reactor Design
The field of high pressure chemical reactors is continuously evolving, with new designs and technologies being developed to address the challenges mentioned above. Some of the latest innovations include:
-
Automated Control Systems: Advances in digital technology have led to the development of automated control systems that can monitor and adjust reaction conditions in real-time. These systems use sensors and feedback loops to maintain optimal conditions, improving both safety and efficiency.
-
Advanced Materials: New materials are being developed that offer greater resistance to corrosion and wear, extending the lifespan of reactors and reducing maintenance costs. For example, reactors made from advanced alloys or coated with specialized materials can handle more aggressive chemicals.
-
Modular Reactor Designs: Modular reactors are designed to be easily scalable, allowing for quick adjustments to capacity based on production needs. This flexibility is particularly valuable in industries where demand can fluctuate, such as pharmaceuticals or specialty chemicals.
-
Green Chemistry Applications: High pressure reactors are increasingly being used in green chemistry applications, where the goal is to develop more sustainable processes. For example, supercritical carbon dioxide is used as a green solvent in certain reactions, reducing the need for harmful organic solvents.
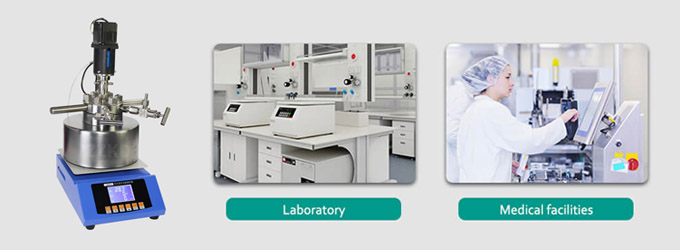
The Future of High Pressure Chemical Reactors
High pressure chemical reactors will continue to play a vital role in various industries, from pharmaceuticals to petrochemicals and beyond. As technology advances, these reactors will become even more efficient, safer, and versatile, opening up new possibilities for chemical synthesis and processing.
Whether used in research labs or large-scale production facilities, high pressure reactors are indispensable tools for driving innovation and improving process efficiency. By understanding their capabilities, applications, and challenges, one can fully appreciate the value they bring to modern chemical engineering.
But with all this knowledge in hand, one must ask: How will future innovations in high pressure chemical reactors reshape the landscape of chemical manufacturing? The answer lies in the continued collaboration between engineers, scientists, and manufacturers to push the boundaries of what these powerful tools can achieve.