In the current era, where environmental sustainability and cost efficiency take center stage, industries are increasingly seeking innovative solutions to address these pressing concerns. One such solution gaining prominence is the solvent recovery machine. This groundbreaking technology not only facilitates the effective recycling of acetone, a widely used solvent, but also contributes to reducing waste, minimizing environmental impact, and optimizing resource utilization. In this article, we will explore the concept of acetone recycling, its applications in various industries, and the significant benefits it offers.
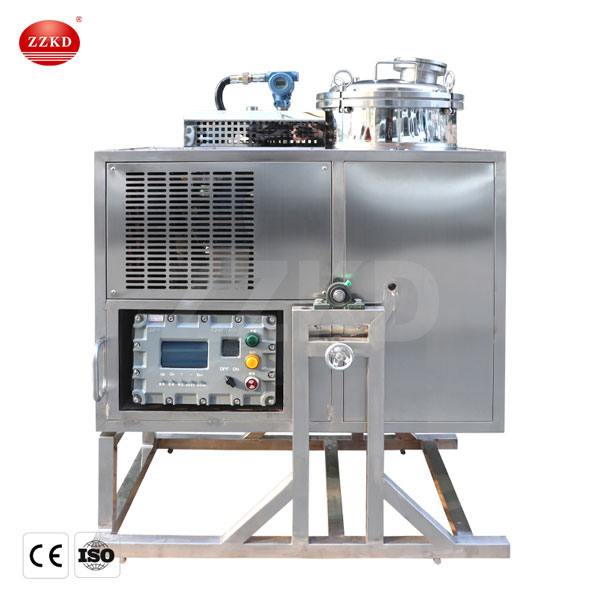
Understanding Acetone Recycling:
Acetone, with its versatile properties, is extensively used in numerous industrial processes, ranging from pharmaceuticals and cosmetics to paints and adhesives. However, traditional practices often involve disposing of used acetone, leading to environmental pollution and wastage. Acetone recycling, on the other hand, involves the collection and purification of used acetone, making it suitable for reuse.This sustainable approach not only conserves resources but also offers substantial cost savings.
The Working Principle of Acetone Recyclers:
Acetone recyclers employ sophisticated technology to recover and purify used acetone. The process typically involves the following steps:
a) Collection: Used acetone is collected from various sources, such as manufacturing processes, cleaning operations, and laboratories. This ensures that acetone, which would otherwise be discarded, is captured for recycling.
b) Purification: The collected acetone undergoes a purification process that removes impurities, contaminants, and other substances. This purification step is crucial in restoring the quality of acetone to a level suitable for reuse.
c) Distillation: Once purified, the acetone is subjected to distillation, a process that separates acetone from other residual compounds. Distillation enables the recovery of high-purity acetone, which can be used in subsequent industrial processes.
d) Quality Control: The final step involves stringent quality control measures to ensure that the recycled acetone meets the required standards. This includes testing for purity, composition, and other specifications.
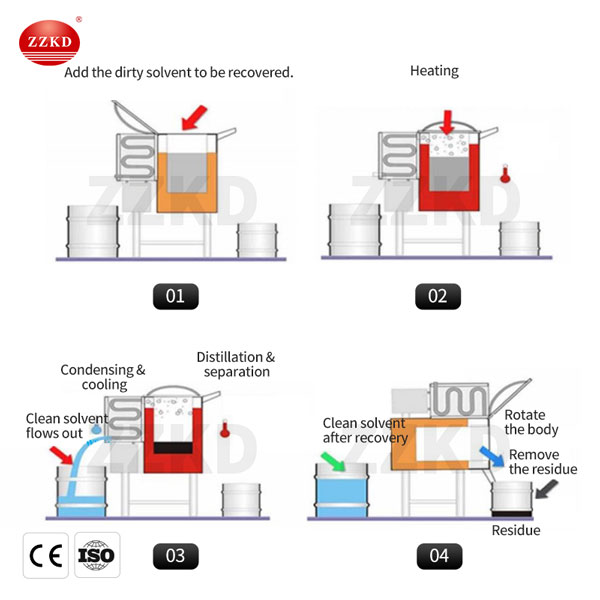
Advantages of Acetone Recycling:
Implementing acetone recycling in industrial processes brings forth several noteworthy advantages:
a) Cost Savings: Acetone recycling significantly reduces procurement costs by eliminating the need for purchasing new acetone for each use. This cost-effective approach translates into substantial savings for industries, especially those with high acetone consumption.
b) Environmental Benefits: By recycling acetone, industries can minimize waste generation and reduce the release of harmful substances into the environment. This leads to a decrease in air and water pollution, preserving natural resources and contributing to a cleaner ecosystem.
c) Resource Optimization: Acetone, a valuable resource, can be conserved and reused effectively through recycling. This not only helps in preserving the availability of acetone but also reduces the demand for its production, leading to a more sustainable and resource-efficient industry.
d) Regulatory Compliance: Acetone recycling aligns with environmental regulations and sustainability initiatives. By adopting this practice, industries can ensure compliance with governmental guidelines, mitigate legal risks, and demonstrate their commitment to responsible and eco-friendly operations.
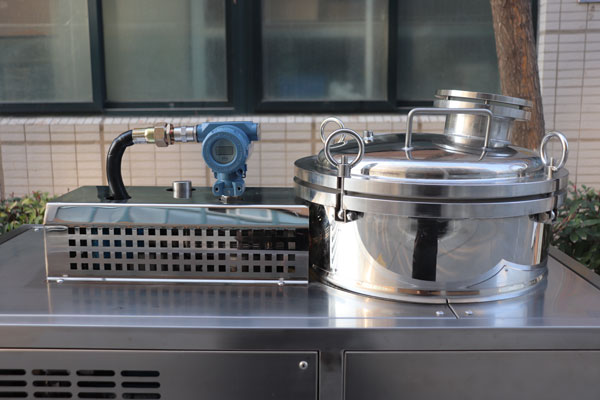
Types of acetone recycler for recovery
1. Aromatic hydrocarbons: toluene, xylene, trimethylbenzene, etc.;
2. Aliphatic hydrocarbons: pentane, hexane, octane, etc.;
3. Alicyclic hydrocarbons: cyclohexane, cyclohexanone, tolyl cyclohexanone, etc.;
4. Halogenated hydrocarbons: chlorobenzene, dichlorobenzene, methylene chloride, trichloroethylene, etc.;
5. Alcohols: methanol, ethanol, isopropanol, etc.;
6. Ethers: ether, propylene oxide, etc.;
7. Esters: methyl acetate, ethyl acetate, n-butyl acetate, etc.;
8. Ketones: acetone, butanone, methyl isobutyl ketone, etc.;
9. And other organic solvents not listed.
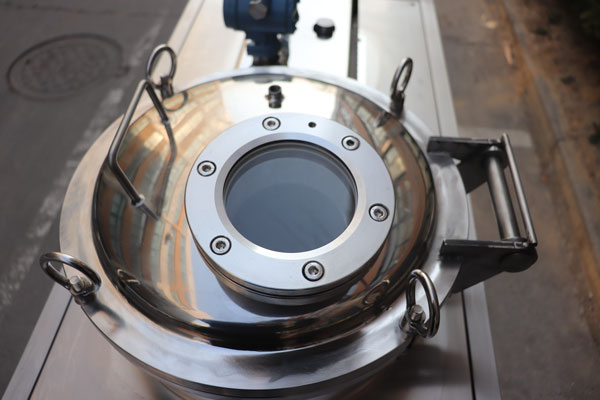
Types of acetone recycler that are not suitable for recovery
1. Dangerous solvents such as nitrocellulose (nitro) and oxidants;
2. Strong acid or strong alkaline solvent;
3. Highly toxic solvents;
4. Solvents that are highly corrosive to stainless steel or copper pipes, etc.
Application Case: Automotive Industry
The automotive industry is one sector where acetone recyclers have found significant application. Automobile manufacturing processes involve the use of acetone-based solvents for various purposes, including surface preparation, adhesive application, and cleaning. Traditionally, these solvents were disposed of after a single-use, resulting in increased costs and environmental impact.
However, with the adoption of acetone recyclers, automotive manufacturers can now recover and reuse acetone, leading to multiple benefits. Firstly, it substantially reduces the procurement costs associated with purchasing new acetone for every production cycle. Secondly, it minimizes waste generation and the need for hazardous waste disposal, aligning with sustainable practices. Lastly, it contributes to the overall reduction of the automotive industry's carbon footprint by conserving resources and reducing energy consumption.
ZZKD hot sale
Paint Solvent Recycling Machine
Model:T-100Ex
Feed capacity(L):100
Power supply(ACV):380
Power(kW):8
Temperature range (℃): 5~200
Treatment time (Min.):240
Recovery(%):95
Solvent recovery machine
Model:T-60Ex
Feed capacity(L):60
Power supply(ACV):380
Power(kW):5
Temperature range (℃): 5~200
Treatment time (Min.):240
Recovery(%):95